A Big Brake For Silicon Carbide In The New McClaren P1
The brand new McLaren PI is probably the most advanced and jaw-dropping car the world has ever seen. With a price tag of £866,000, the attention to detail in the car is almost science fictional and, as you’d expect, it is made from all sorts of exotic materials beneath its mostly carbon fiber outer skin. The combination of these result in a kerb weight of just 1,450kg which is less than a Vauxhall Astra!
The new P1 is propelled by two distinctly different power sources. The first is a twin-turbo 3.8-litre V8 engine that produces 727bhp at 7,300rpm. The second involves an electric motor that uses a brace of lithium ion batteries to produce a further 176bhp. This provides the rear-wheel-drive P1 with an astonishing combined output of 903bhp, enough to fire it to 60mph in just 2.8sec, to 100mph in well under 6 seconds and to 200mph in under 20sec.
“…The wheels are made from military grade aluminium and the brake discs from a material that’s only ever been used in France’s Ariane Space Programme. They’re coated with something called silicon carbide which is apparently the hardest substance known to man – apart from dried Weetabix obviously! …”
At Precision Ceramics, we would whole-heartedly agree that silicon carbide is one of the hardest materials known to man (definitely not dried Weetabix) but is definitely not the hardest. That role goes very firmly to diamond but there are other technical ceramics which would also qualify.
Top of the list is boron carbide which ranks third behind diamond and cubic boron nitride. Originally discovered in the mid-nineteenth century, boron carbide is nowadays the hardest material produced in tonnage quantities.Boron carbide is characterised by several unique properties …
- Extreme hardness
- Difficult to sinter to high relative densities without the use of sintering aids
- Good chemical resistance
- Good nuclear properties
- Low density
The extreme hardness of boron carbide provides excellent wear and abrasion resistance and consequently it is a perfect base material for the manufacture of nozzles for slurry pumping, grit blasting and in water jet cutters.
In combination with other materials, boron carbide also finds extensive use in ballistic armour (including body and personnel armour) where its combination of high hardness, high elastic modulus, and low density gives the material an exceptionally high specific stopping power to defeat high velocity projectiles.
Other applications include ceramic tooling dies, precision tool parts, evaporating boats for materials testing and mortars and pestles.
At Precision Ceramics, both boron carbide and silicon carbide are used as a base material for a wide range of technical components for an equally wide field of applications.
Like both oxides and nitrides, silicon carbide is a very hard wearing material, which requires diamond-grinding methods to process once fired. Although not exclusively, carbides are used mainly for applications in which physical wear is a major consideration.
So for coating the brake discs in what is probably the world’s most advanced and jaw-dropping car, silicon carbide is certainly a good choice. This said, Mr Clarkson, it’s not the hardest!
Related Topics
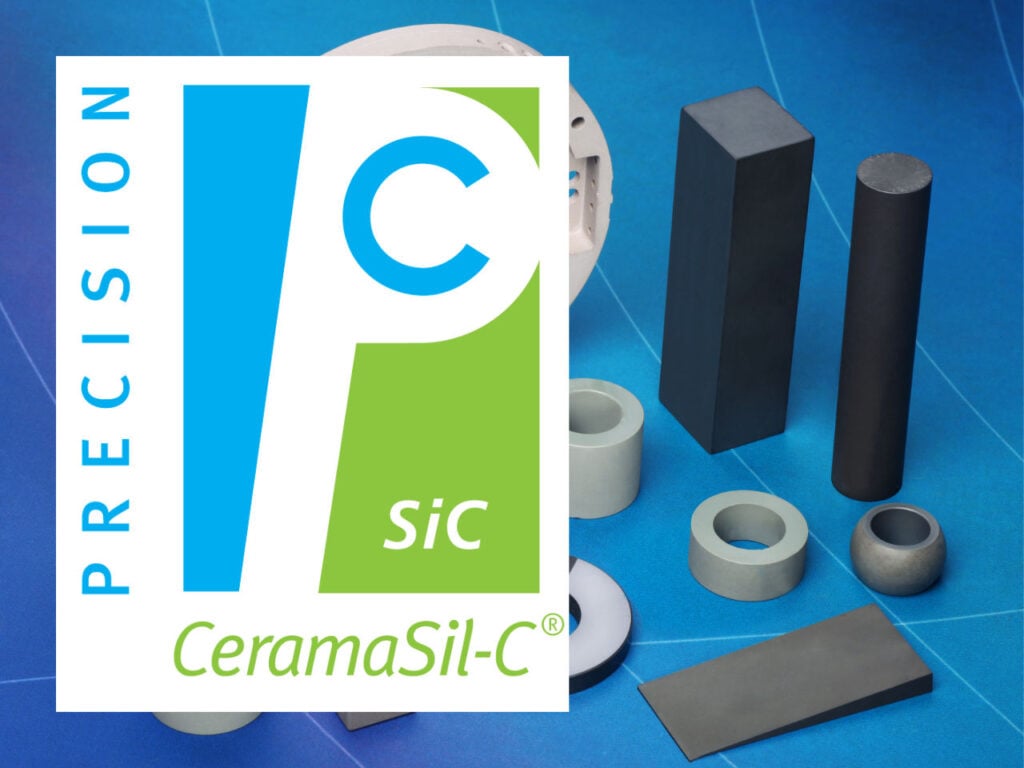
Silicon Carbide
CeramaSil-C™
Silicon Carbide (SiC) is one of the lightest, hardest, and strongest technical ceramic materials with exceptional thermal conductivity, acid resistance, and low thermal expansion.
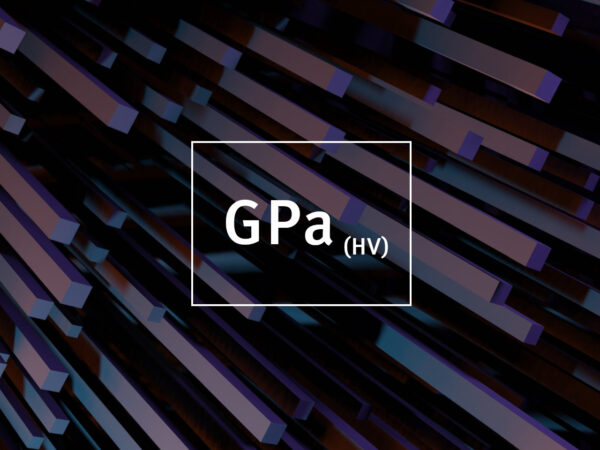
Hardness
One of the most valuable characteristics of advanced ceramics in high-performance applications is their extreme hardness. Hard ceramic materials are used for a wide range of applications in diverse fields and applications such as cutting tools for milling and grinding.