In the second in a series of blogs, Geoff Randle, Precision Ceramics Business Director, reflects on the use of advanced ceramics for ultra-high vacuum applications.
“The first time I heard the expression ‘ultra-high vacuum’, I was sitting in a meeting looking at drawings dated 1963 and was asked if the parts in the drawing complied. Luckily my colleague was on the ball and I did not have the embarrassing ‘Dyson’ moment I could have had! In hindsight, that would more likely have been a ‘Hoover’ moment back in the 1970’s!
Ultra-high vacuum is stated to be 10-9 torr and this level of vacuum is used by scientists to conduct specialised experiments by removing all of the gases that may detract from and invalidate their experiments or by preventing the conditions under which the electrical part of the experiment can operate.
Having to conduct experiments under vacuum presents a number of problems. Initially you have to create a chamber that can hold the required level of vacuum. At the same time, you need to be able to place the materials you are researching into the chamber before conducting the experiment. A requirement for power to be available within the chamber is also often necessary.
For research applications like these, advanced ceramics are the ideal solution and come into their own when high voltage electrical insulation is required along with zero outgassing of the ceramic in the vacuum. Ceramics bonded to metals also provide the opportunity to enable power or signals to be transferred through the wall of the vacuum vessel without electrifying the wall.
Metal containers can range in size from a small benchtop unit to a large building and in the case of the syncotron beam facility can stretch over hundreds of metres of tubes and vessels with ports to give manual and visual access into the chamber and special pumps to create the vacuum.
There are many different types of ceramic that can be used within the chamber but all of them must have zero outgassing (to avoid chemical components being shed by the ceramic and confusing the experiment), zero porosity (as highly porous materials would require long pumping times to achieve vacuum) and good electrical insulation. Other factors may apply such as thermal conductance, mechanical strength and being inert to magnetic fields.
The chambers tend to be built from steel and, dependent on the level of complexity, the cost of these analysis machines can range from thousands for a small bench top model to millions of pounds for specialist top end machines.
Some of the largest facilities are made to test satellites where the whole satellite is placed in a vacuum chamber to replicate conditions in space and space flight conditions for testing electric thrusters.”
Ultra high vacuum is difficult to maintain in our atmosphere but is invaluable to science and research.
Geoff Randle is a specialist in advanced ceramics in a career spanning 40 years. He is a director of both McGeoch Technology and Precision Ceramics. Geoff also became an Executive Vice President of Precision Ceramics USA when the first overseas subsidiary of the company was formed in Tampa, Florida, 2009.
Related Topics
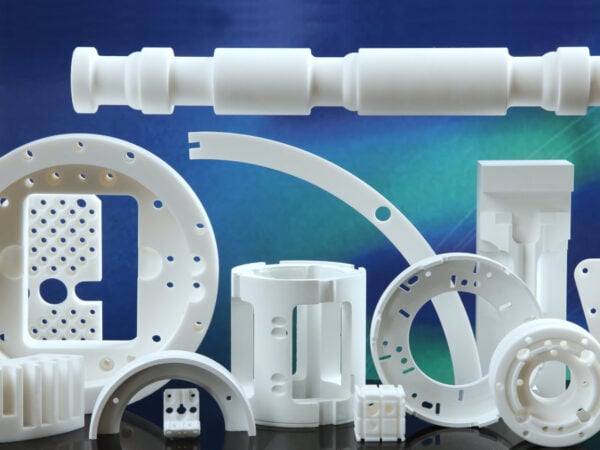
Materials
Precision Ceramics offers a wide range of advanced ceramic materials. We can help with the engineering tolerances, design for manufacture, selection of the materials and application environment questions.