Hall Effect Thrusters were originally conceptualized in 1911 and began being implemented in the 1950’s and now are the main method of satellite propulsion in space.
The move away from flammable propellant has spawned a wide array of propulsion technologies, with improved safety and lower launch weights; Hall Effect and Ion thrusters being only two of the technologies, for the positioning, station keeping, and even interplanetary exploration markets.
Hall Effect Thrusters use inert gases as the propellant, typically but not exclusively Xenon. Other options are Iodine, Argon and Krypton. The use of these types of gases removes the possibility of accidental flammable explosion and reduces the initial launch weight of the satellite. The popularity of some of these gases has caused significant increases in gas costs, because of the number of satellites now being used.
The electrical power of the satellite is developed from solar arrays. This provides power for the satellite operation and propulsion. The propulsion requires ionized gases to be propelled at high speeds between 10 to 50 kilometers per second. The ionized gas is propelled from the anode to the cathode by the electrical potential over the ceramic insulator.
The effectiveness of a Hall Effect Thruster depends on the electrical insulation properties of the ceramic. The ceramic must be low weight and capable of withstanding impact from stray ions and be an excellent electrical insulator.
Precision Ceramics offers a wide range of ceramic options for the channel and electrical isolation within the satellite. Ceramics used for the channel range from the latest AlN/BN composites to Boron Nitride materials, all with a pedigree of use in space from small LEO satellites to large complex interplanetary missions. The Channels range in size and geometry and can be machined either at our USA or UK facility.
Insulators within the satellite can be made from Alumina, in various grades small prototype batches up to full production. Macor can be used for more complex components requiring tight tolerances that would be difficult to grind in Alumina.
Small batches for development trials can be produced as we have Alumina production in-house and a full range of Macor machining.
The life of a satellite held in orbit can be constrained by the amount of propellant, the lifetime of the ceramic, or the lifetime of the technology the satellite supports. The rapid changes in technology have driven a massive increase in the number of satellites employed.
For more information, see our material selection for Channels here!
Related Pages
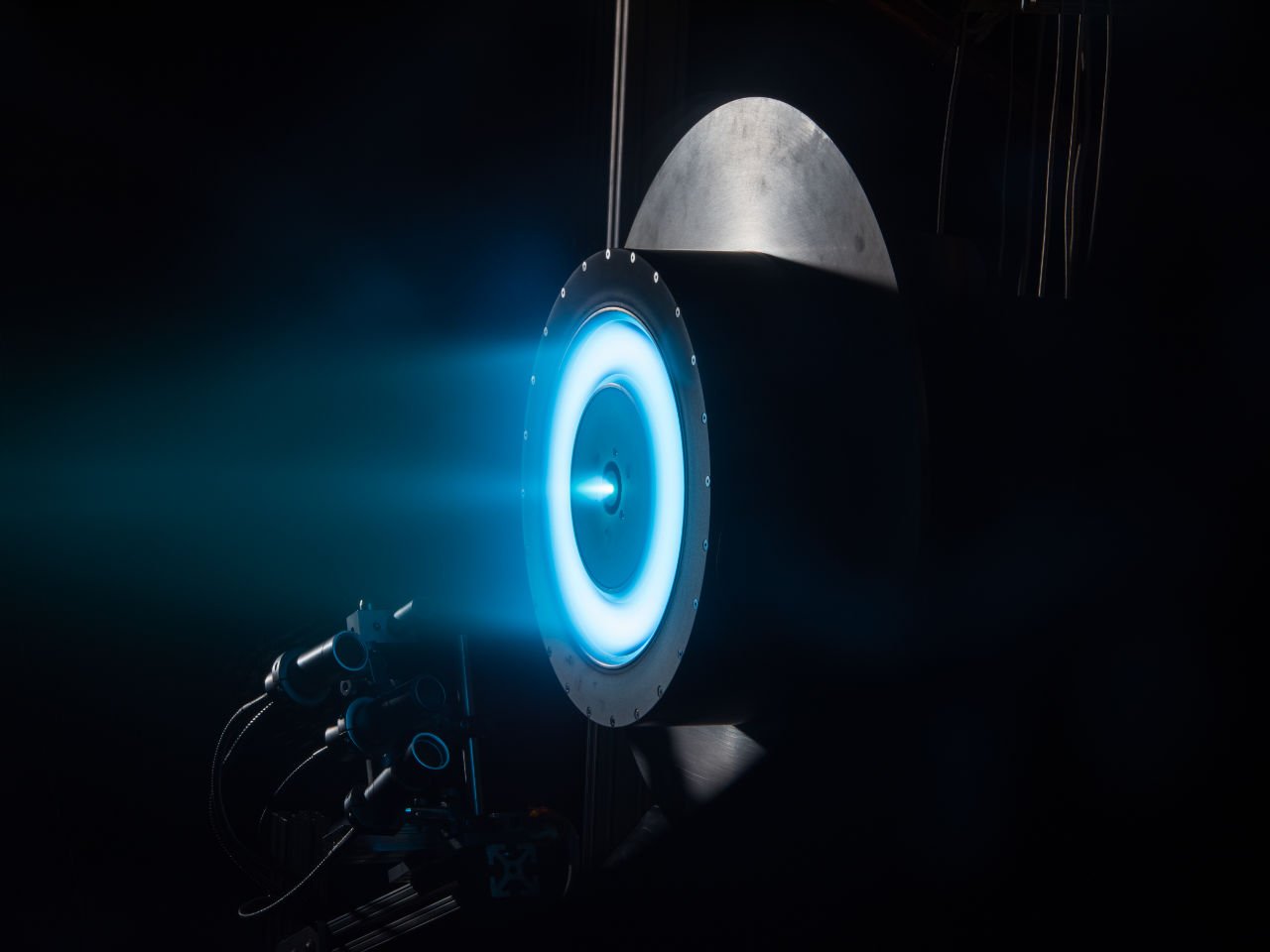
Hall Effect Thrusters
Precision Ceramics has over 30 years’ experience working with ceramic materials providing channels in differing grades of material from 12 mm to over 300 mm diameter.