Nel mondo della ceramica tecnica ci sono due materiali che in termini di durezza sono superati solo dal diamante e dal nitruro di boro cubico, ed entrambi vengono utilizzati da Precision Ceramics USA come materiale di base per un’ampia gamma di componenti tecnici in un campo di applicazioni altrettanto ampio.
Il carburo di boro (B 4 C) è attualmente il materiale più duro prodotto in quantità di tonnellate ed è il terzo materiale più duro conosciuto dall’uomo dopo il diamante e il nitruro di boro cubico. Non molto dietro in termini di durezza c’è il carburo di silicio (SiC) , intriso di storia da quando è stato prodotto in serie per la prima volta nel 1893 e probabilmente il più comune di tutti gli abrasivi industriali.
La B4C
L’estrema durezza del carburo di boro garantisce un’eccellente resistenza all’usura e all’abrasione e,
di conseguenza, è un materiale di base perfetto per la fabbricazione di ugelli per il pompaggio di fanghi, ghiaia
sabbiatura e taglio a getto d’acqua.
In combinazione con altri materiali, il carburo di boro trova ampio impiego anche nelle armature balistiche (comprese quelle per il corpo e per il personale), dove la combinazione di elevata durezza, elevato modulo elastico e bassa densità conferisce al materiale un potere d’arresto specifico eccezionalmente elevato per contrastare proiettili ad alta velocità.
Altre applicazioni includono stampi per utensili in ceramica, parti di utensili di precisione, maschere e altri materiali ad alta usura.
applicazioni.
Silicio
Le proprietà tecniche del carburo di silicio sono notevolmente simili a quelle del diamante. È uno dei materiali ceramici tecnici più leggeri, duri e resistenti e ha un’eccezionale conduttività termica, resistenza chimica e bassa dilatazione termica.
Il carburo di silicio è un materiale eccellente da utilizzare quando l’usura fisica è un fattore importante da considerare, perché offre una buona resistenza all’erosione e all’abrasione, rendendolo particolarmente adatto per applicazioni quali ugelli di spruzzatura, ugelli di granigliatura e componenti di cicloni.
Non molto tempo fa, il carburo di silicio era il materiale scelto per rivestire i freni delle auto più avanzate e spettacolari che il mondo abbia mai visto, come ad esempio la McLaren P1.
Precision Ceramics ha sviluppato anche una gamma di altri materiali da aggiungere alla nostra collezione di materiali ultraduri.
DuraWear , un ibrido che unisce i vantaggi del carburo di boro ( B4C ) e del carburo di silicio (SiC) , questo materiale si è evoluto per mantenere l’incredibile durezza di entrambi i materiali, senza alcuni dei vincoli di entrambi. Questo ibrido offre i vantaggi di un punto di fusione elevato, una buona resistenza agli shock termici ed è chimicamente inerte.
DuraShock TM , un ibrido che combina sempre B4C e SiC, ma focalizzato sulle applicazioni balistiche, questo materiale leggero ma incredibilmente duro può resistere ad alcune delle minacce più recenti, pur essendo molto più facile da produrre rispetto al puro carburo di boro pressato a caldo.
CeramAlloy Ultra Hard, una Zirconia Toughened Alumina (ZTA), una ceramica ossidica, questo materiale combina un’elevata durezza con una buona tenacità alla frattura e una buona resistenza alla flessione. Il materiale è anche “hipped” (Hot Isostatic Pressed), un processo che applica una pressione estrema e un’alta temperatura allo stesso tempo, migliorando ulteriormente il materiale e conferendogli un’eccellente consistenza.
Il nostro processo di Hipping interno viene utilizzato con molti dei nostri materiali ultra-duri e ultra-resistenti per resistere
quei materiali ad un altro livello.
Questi materiali sono ben esposti sugli scaffali dei magazzini di materie prime di Precision Ceramics. Ed è per questo che continuano a fornire il massimo livello di prestazioni ai clienti di Precision Ceramics USA in tutto il mondo in un ampio campo di applicazioni.
Lassù è dura…
E per essere al top, bisogna essere duri. Questi materiali sono esposti in alto sugli scaffali del Precision
Magazzini di materie prime ceramiche. Ecco perché continuano a fornire il livello più alto di
prestazioni ai clienti di Precision Ceramics in tutto il mondo in un ampio campo di applicazioni.
Ulteriori informazioni tecniche e applicative dettagliate, nonché schede tecniche scaricabili per tutti i nostri materiali, sono disponibili sul sito web di Precision Ceramics USA.
La tabella dati sottostante confronta la durezza e la tenacità alla frattura (con valori indicativi) dei 4 materiali menzionati.
ID | composto | Durezza | Tenacità alla frattura |
---|---|---|---|
Carburo di boro | B4C | 35V 0,5 [GPa] | 2 K CI [MPa/m2] |
Carburo di silicio | Silicio | 25 Volt 0,5 [GPa] | 3,5 K CI [MPa/m2] |
Carburo di boro-carburo di silicio (DuraWear) | Composito B 4 C / SiC | 31V 0,5 [GPa] | 3,4 K CI [MPa/m2] |
Carburo di silicio-carburo di boro (DuraShock TM ) | Composito SiC/ B4C | 28V 0,5 [GPa] | Circuito integrato da 4K [MPa/m2] |
Allumina rinforzata con zirconia (CeramAlloy) | ZTA | 16V 0,5 [GPa] | 7K CI [MPa/m2] |
Visualizza la gamma completa di materiali ceramici offerti da Precision Ceramics USA.
Argomenti correlati
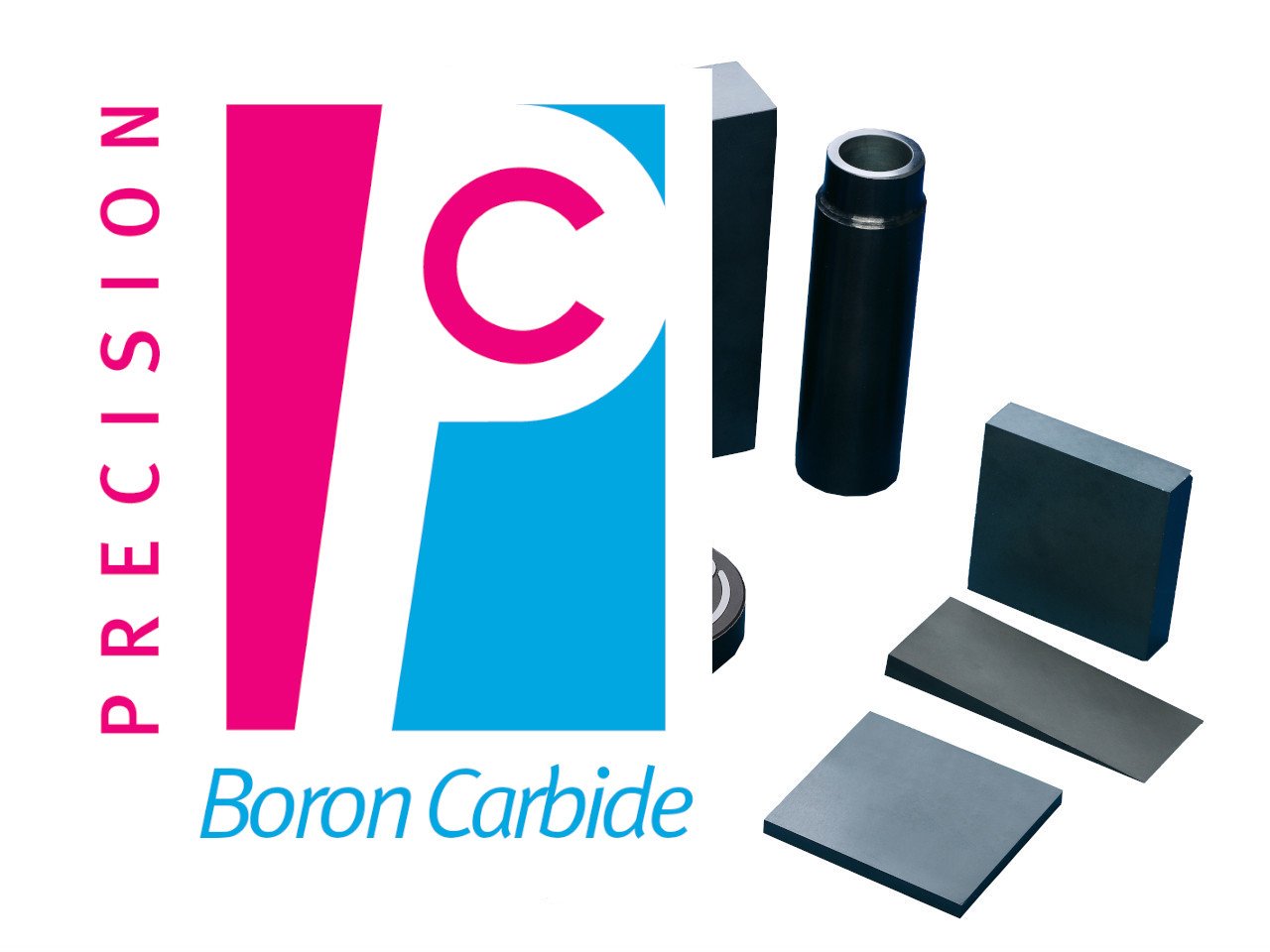
Carburo di boro
DuraShock™ e DuraWear™
Il carburo di boro (B4C), noto anche come diamante nero, è il terzo materiale più duro dopo il diamante e il nitruro di boro cubico. È un materiale adatto a molte applicazioni ad alte prestazioni grazie alla sua attraente combinazione di proprietà.
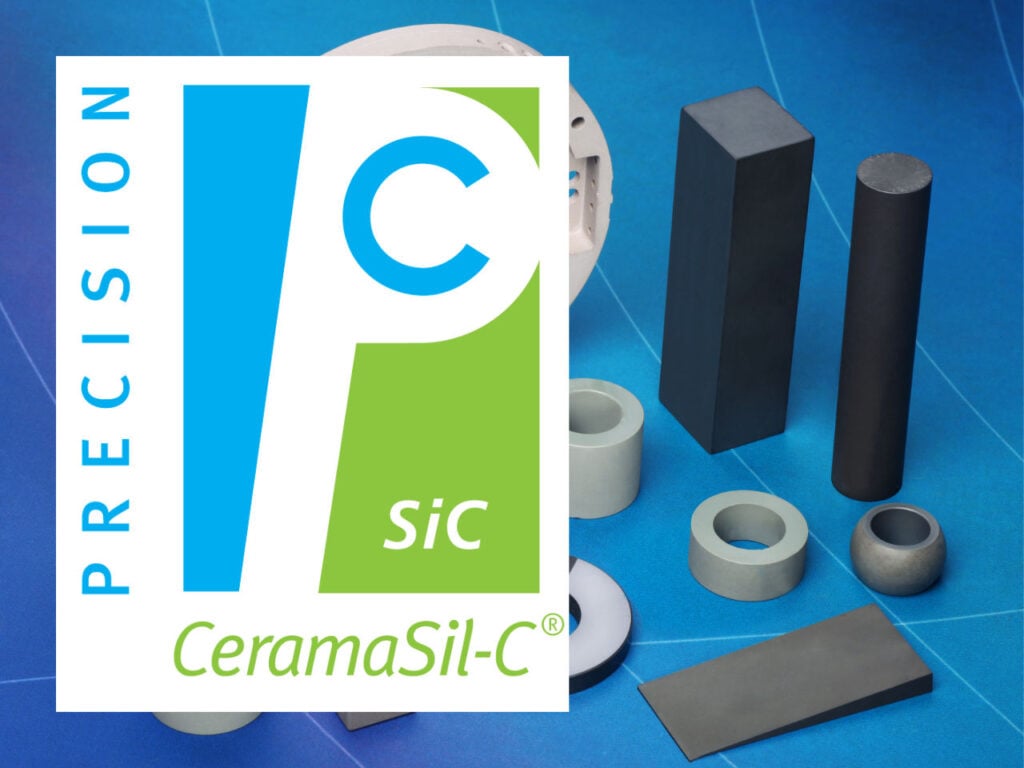
Carburo di silicio
CeramaSil-C™
Il carburo di silicio (SiC) è uno dei materiali ceramici tecnici più leggeri, duri e resistenti, con eccezionale conduttività termica, resistenza agli acidi e bassa dilatazione termica.
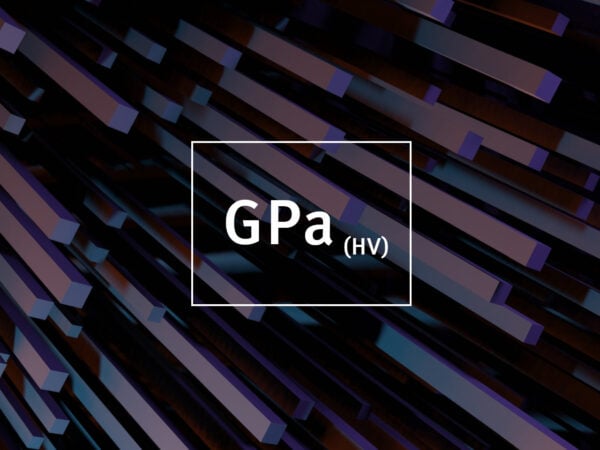
Durezza
Una delle caratteristiche più preziose della ceramica avanzata nelle applicazioni ad alte prestazioni è la sua estrema durezza. I materiali ceramici duri trovano impiego in un'ampia gamma di applicazioni in diversi campi e applicazioni, come ad esempio utensili da taglio per la fresatura e la rettifica.

Tenacità alla frattura
La capacità di resistere alla frattura è una proprietà meccanica dei materiali nota come tenacità alla frattura. Per le ceramiche avanzate utilizza un fattore di intensità di stress critico noto come KIC, dove la frattura avviene normalmente alle terminazioni delle crepe.