Ceramics for Fusion: Advancing Clean Energy
Ceramic Materials used in Fusion Reactors
Ceramics, such as Shapal Hi M Soft, Macor, Alumina, Boron Nitride, and Zirconia, are utilized in various components, including plasma-facing materials, insulators, and structural components. Their high melting points and ability to withstand neutron bombardment making them ideal candidates materials for maintaining integrity and performance under such harsh conditions.
Additionally, ceramics’ low electrical conductivity helps prevent interference with the reactor’s magnetic confinement systems. Advances in ceramic materials are essential for improving the durability, efficiency, and overall feasibility of fusion reactors as a reliable energy source.
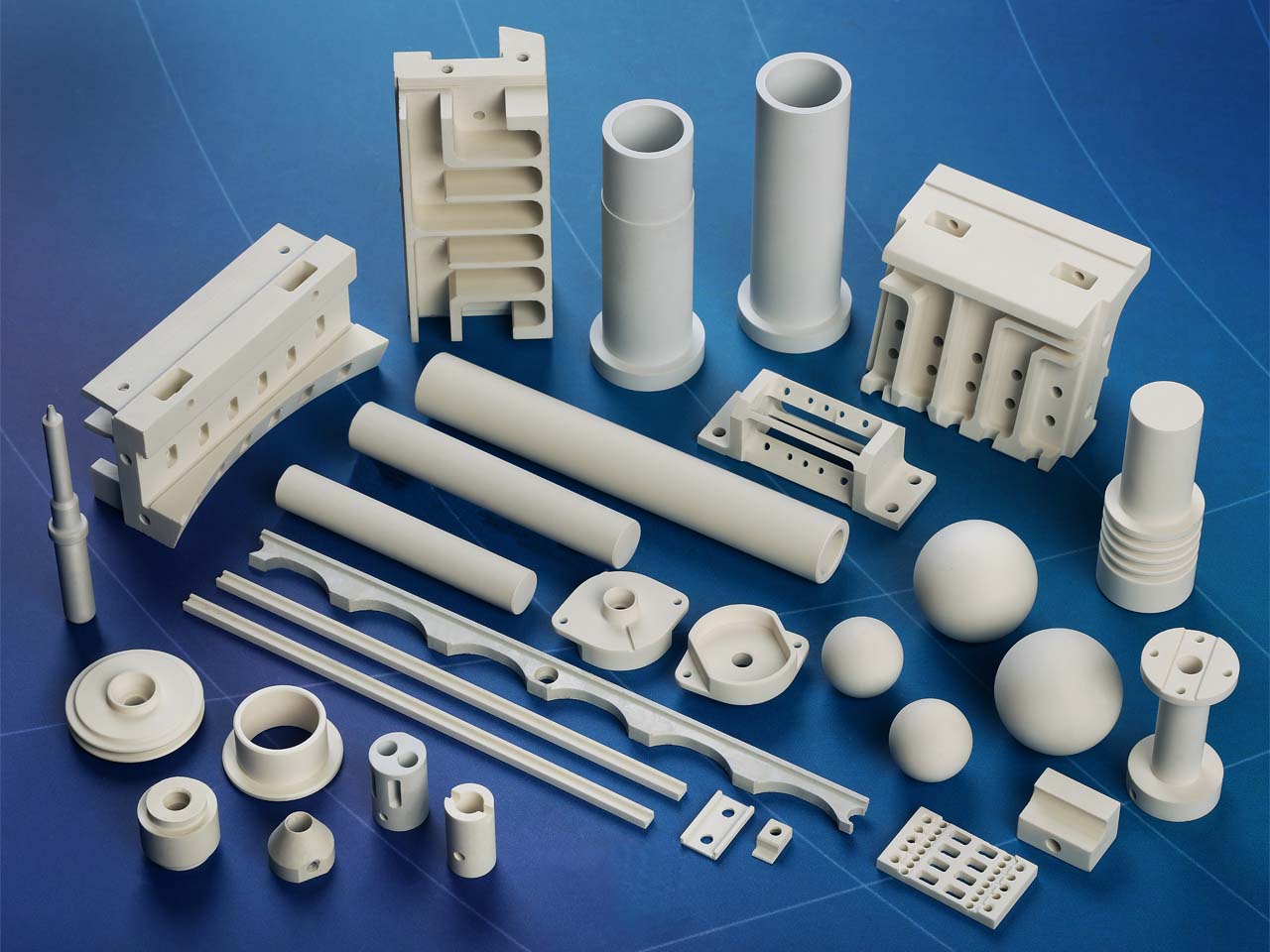
Shapal Hi M Soft™
Machinable AlN
Shapal Hi M Soft is a hybrid type of machinable Aluminium Nitride (AlN) ceramic that offers high mechanical strength and thermal conductivity.
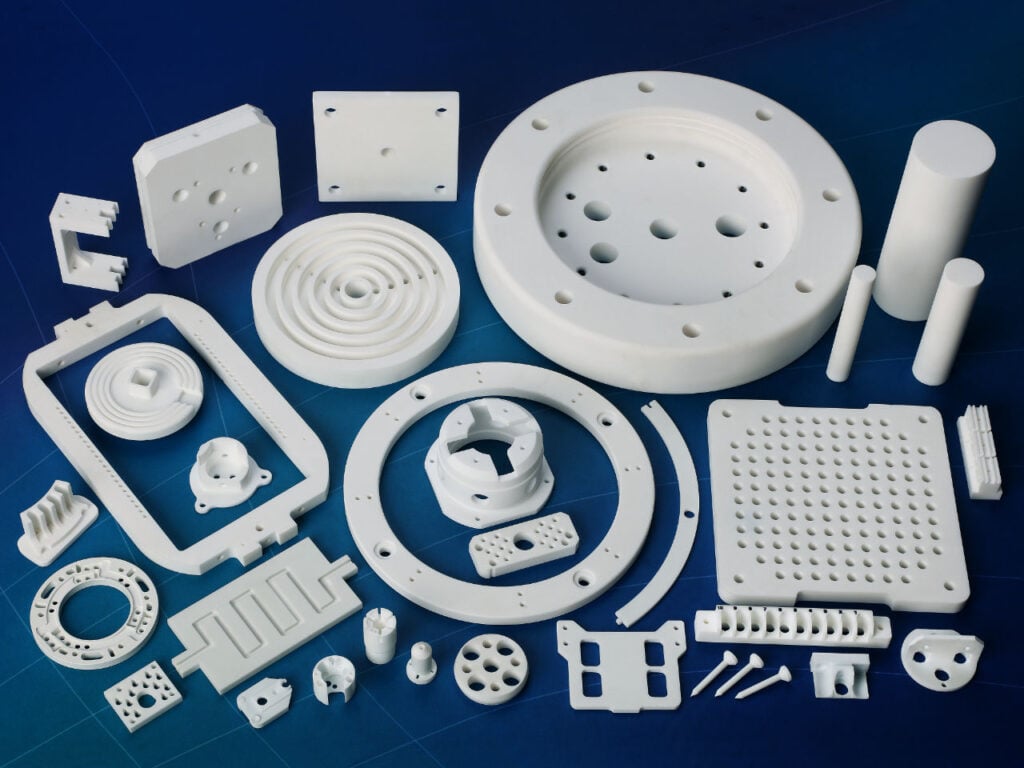
Macor®
Machinable Glass Ceramic
Macor is a hybrid glass-ceramic with the versatility of a high performance polymer, the machinability of a metal, and the performance of an advanced technical ceramic.
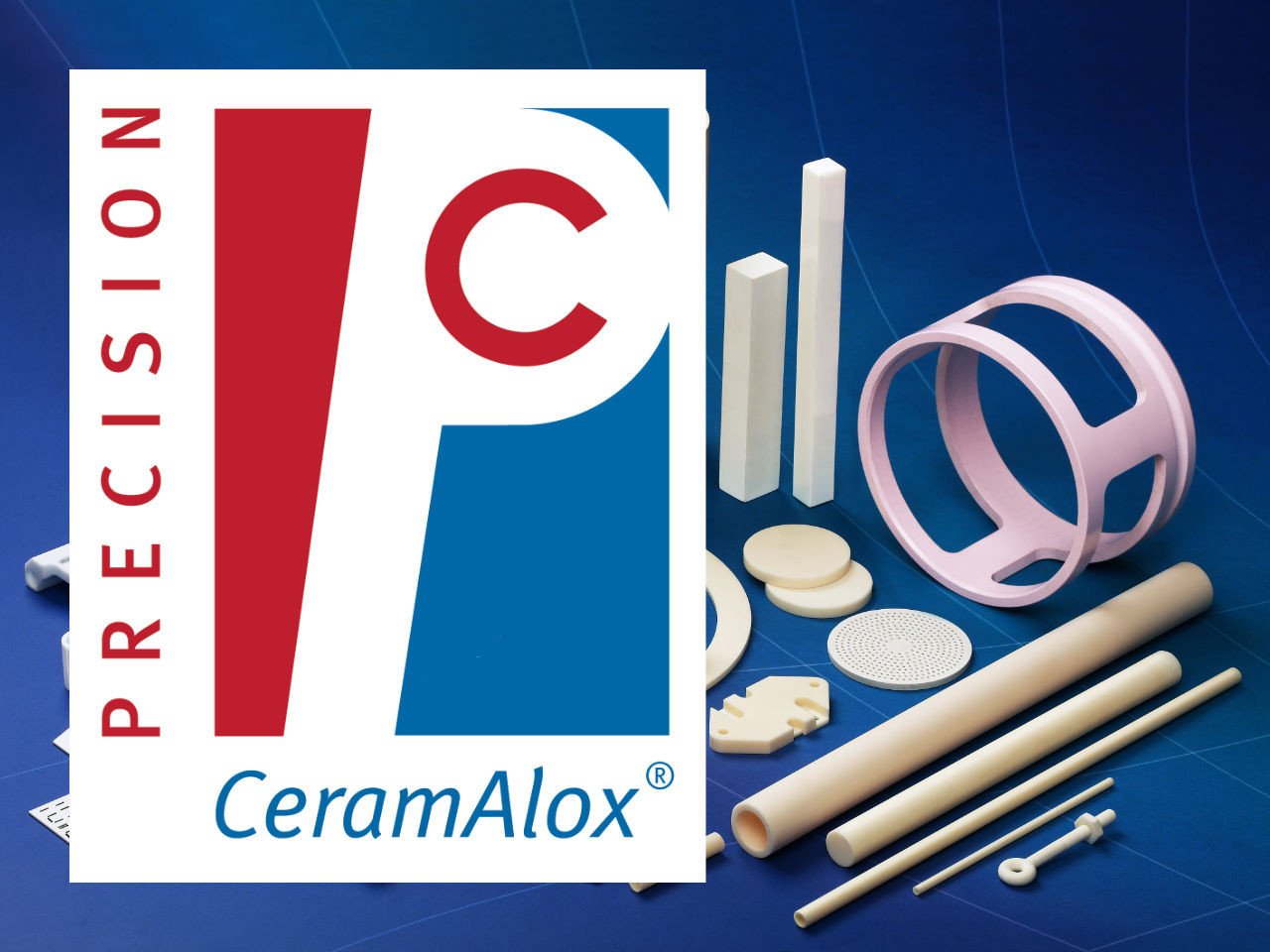
Alumina (Aluminium Oxide)
CeramAlox™
Alumina, also known as Aluminium Oxide, is a hard wearing advanced technical ceramic material frequently used in a wide variety of industrial applications.
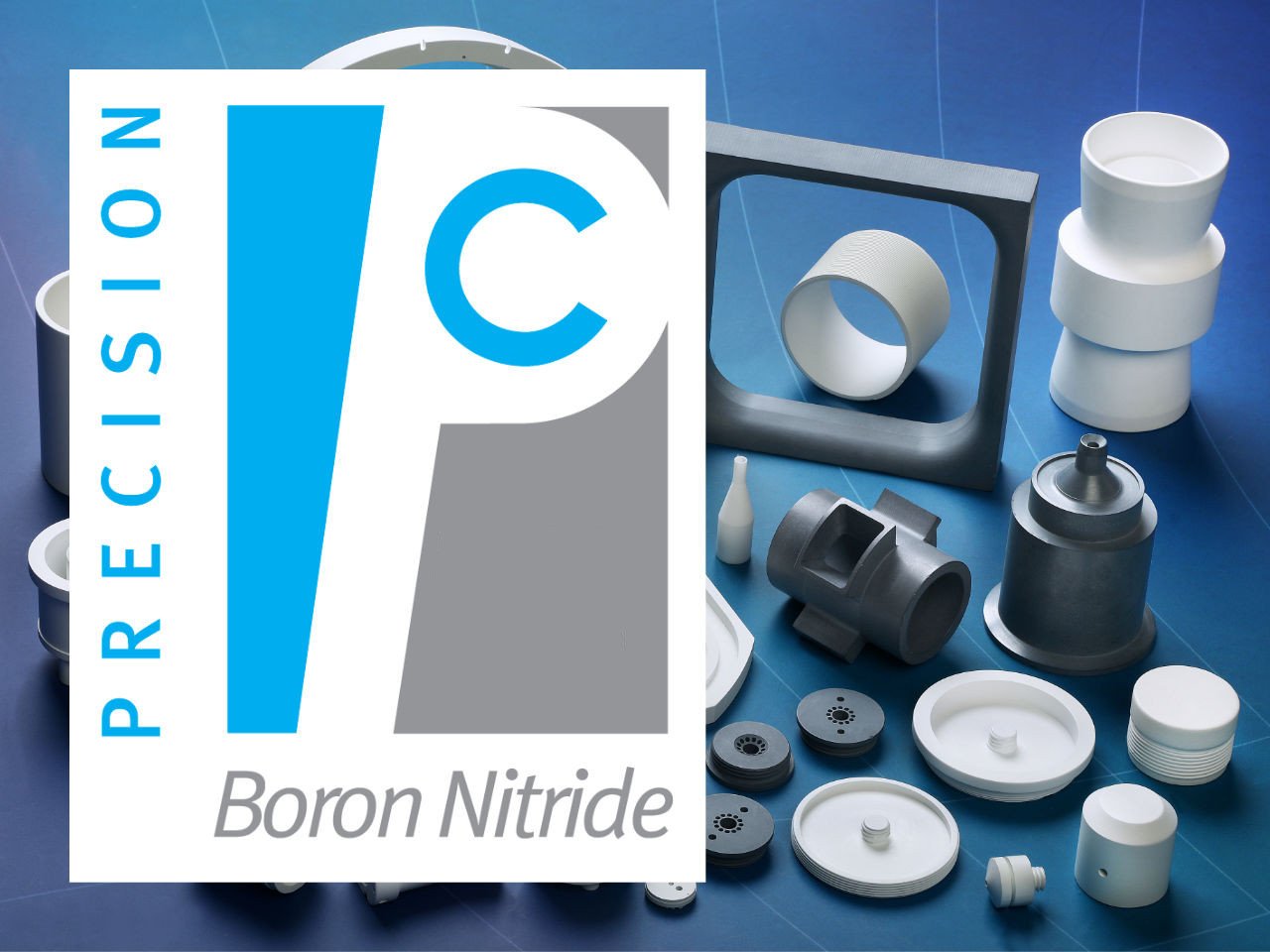
Boron Nitride
Boron Nitride Grades
Boron Nitride (BN) is an advanced synthetic ceramic material available in solid and powder form. It has outstanding thermal conductivity and is easy to machine.
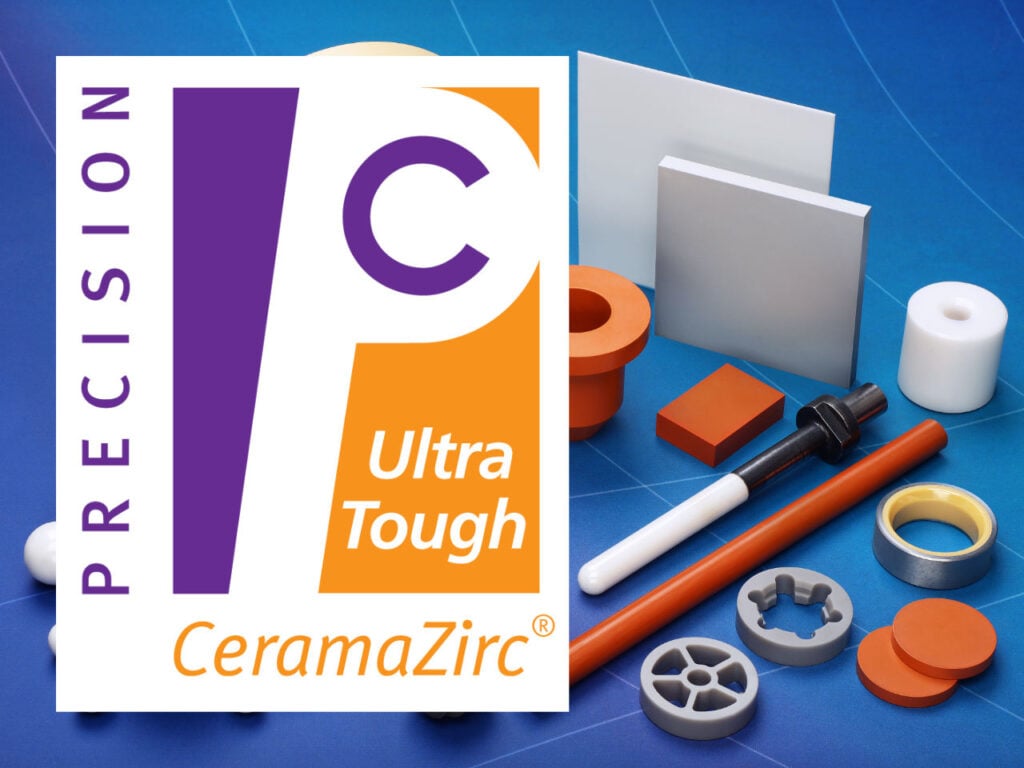
Zirconia
CeramaZirc™
Unlike traditional ceramics that tend to be hard and brittle, Zirconia offers high strength, wear resistance, and flexibility far beyond those of most other technical ceramics.
Precision Ceramics and Fusion

Environments
We supply ceramics for the following environments:
- Ultra-High Vacuum
- High temperature
- High magnetic field
- Radioactive environments
- High energy systems
- Cryogenic temperatures
- Corrosive environments

Applications
The following are typical applications of ceramics in Fusion:
- Radiation shielding
- Thermally conductive ceramics
- Thermally insulating ceramics
- Radiation stable
- High electrical insulation
- High temperature ceramics
- Corrosion and permeation resistance
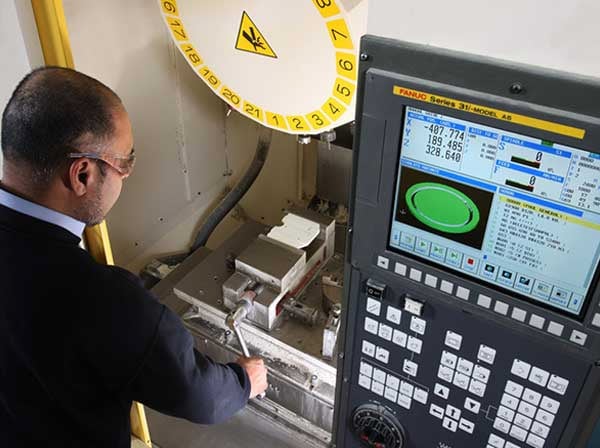
Why Precision Ceramics?
We can offer the following:
- Custom design support
- Quick turnaround
- High tolerances
- Material integrity
- Bespoke ceramic components
- Small to large quantities
- Complex geometries
- Machining with 4th/5th Axis machines
- CNC and multi-axis grinding
- Manufactured in-house
Current Developments in Fusion
The current scale of nuclear fusion research is extensive and global, involving a collaborative effort from numerous countries, institutions, and private companies. The most prominent and ambitious project is the International Thermonuclear Experimental Reactor (ITER) in France, an international collaboration involving 35 countries, including the European Union, the United States, Russia, China, Japan, South Korea, and India. ITER aims to demonstrate the feasibility of sustained fusion reactions on a large scale and is expected to achieve full fusion power operations in the 2030s.
In addition to ITER, several other significant projects and experimental reactors are underway. For instance, the Wendelstein 7-X in Germany is the world’s largest stellarator, designed to test the stability and efficiency of the helical fusion concept. In the United States, the National Ignition Facility (NIF) focuses on inertial confinement fusion and has achieved record-breaking energy yields in its experiments.
Private companies are also increasingly involved in fusion research, with firms like Commonwealth Fusion Systems, TAE Technologies, Zap Energy, and Helion Energy working on innovative approaches to achieve practical and economically viable fusion energy. These companies are exploring various fusion reactor designs and technologies, such as compact tokamaks, Z-pinch, field-reversed configurations, and magnetized target fusion.
Overall, the scale of nuclear fusion research encompasses a wide range of scientific, engineering, and technological efforts aimed at overcoming the substantial challenges to make fusion a viable and sustainable energy source. Significant progress has been made, but substantial technical and economic hurdles remain before fusion can be commercially deployed.
For more information on the pursuit of nuclear fusion and details on the several different approaches see; Exploring Different Types of Nuclear Fusion.
Datasheets
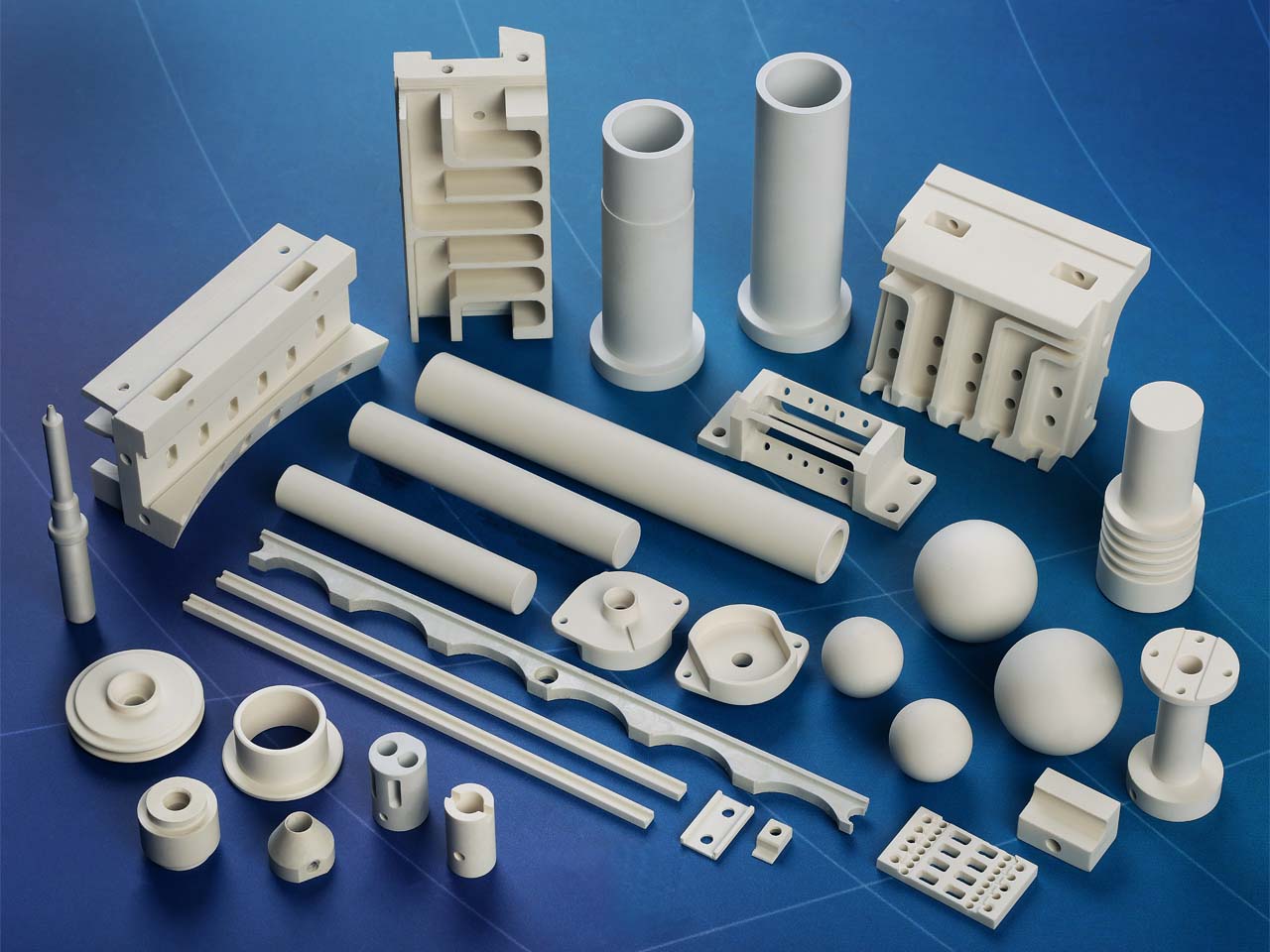
Shapal Hi M Soft
Machinable Aluminium Nitride
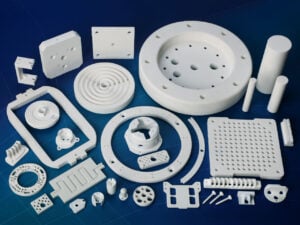
Macor
Machinable Glass Ceramic

Alumina
CeramAlox
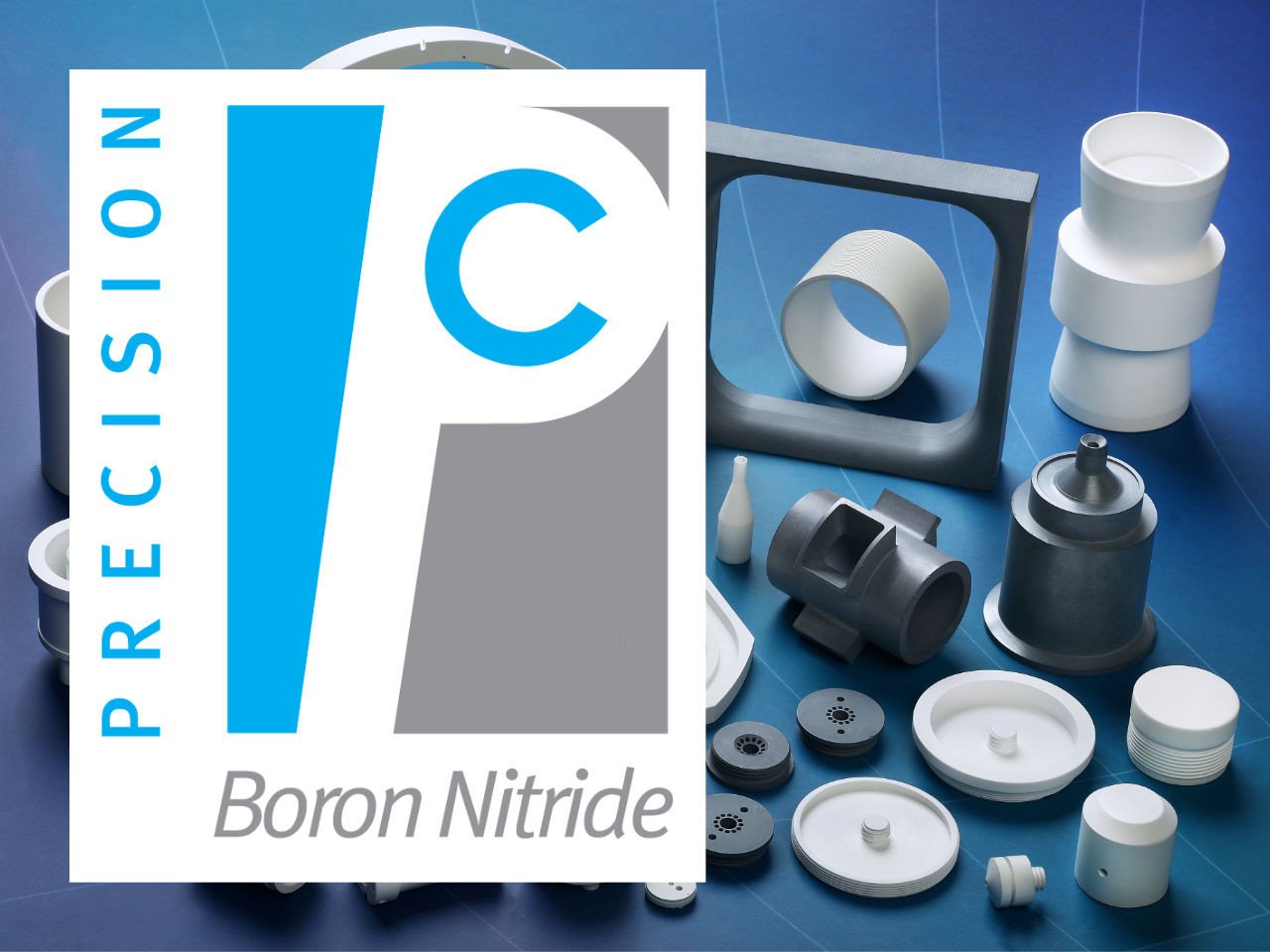
Boron Nitride
Boron Nitride Grades

Zirconia
CeramaZirc Ultra Tough
Frequently Asked Questions
-
Can ceramics withstand fusion reactor conditions?
Technical ceramics are promising candidates for components within a fusion reactor, but not necessarily the core plasma chamber. The combination of advantageous properties that ceramics offer is helpful in extreme environments. Here’s a breakdown:
- Advantages:
- High and low temperature resistance: Certain ceramics can withstand very high temperatures, which is a crucial requirement for fusion reactors. Ceramics are also compatible with cryogenic temperatures.
- Electrical insulation: Most engineering ceramics have excellent insulation properties whilst the thermal properties can be insulating or conducting to suit the application.
- Corrosion and radiation resistance: Ceramics are chemically inert and offer good resistance to radiation environments. Some ceramic materials can be used for radiation shielding.
- Compatible with strong magnetic fields: This enables ceramic components to be used without disturbing the magnetic confinement system.
- Mechanical and dimensional capabilities: Technical ceramics offer high strength and toughness and can be manufactured to high tolerances, offering robust and long life performance required in fusion systems.
- Lithium-containing ceramics: are being researched for their potential role in tritium breeding, a typical process in fusion reactors.
- Challenges:
- Toughness: Ceramics have lower toughness than metals and this needs to be considered in component design and material selection to ensure compatibility in the harshest environments of a fusion reactor.
- Radiation effects: Exposure to radiation in a fusion reactor can degrade the properties of ceramics over time. Conventional ceramic materials would not survive the highest neutron flux levels.
- Manufacturing limitations: Producing complex shapes and large sizes from ceramics can be difficult and expensive. This can limit their use in some applications within a fusion reactor.
- Advantages:
-
How are ceramics used in tokamak reactors?
While conventional ceramics may not be ideal for the superheated and high neutron flux core of a tokamak reactor, they are being explored for specific components in fusion systems. E.g. the breeder blanket, magnetic confinement system, water cooling, electrical and sensor control, high power energy sources for inertial confinement systems etc.
The breeder blanket for example, surrounds the plasma chamber and performs several key functions:
- Tritium Breeding: Fusion reactors typically use a fuel mixture of deuterium and tritium. Tritium is not readily available in nature, so the reactor needs to breed its own tritium fuel. Lithium-containing ceramics are being investigated as a potential material for the blanket. These ceramics would contain lithium, which can be bombarded by neutrons from the fusion reaction to generate tritium.
Here’s how it works:
- Neutrons from the plasma chamber hit the lithium in the ceramic blanket.
- The neutrons cause the lithium to undergo nuclear reactions, producing tritium.
- The tritium can then be extracted and used as fuel for the fusion reaction.
This is still under development, but it highlights a potential application of ceramics in tokamak reactors.
-
What are the limitations of ceramics for fusion?
Ceramics offer multiple advantages for fusion reactors, although limitations need to be recognized to ensure that they are used in suitable applications. Here’s a breakdown of the key limitations:
- Toughness: This is a major consideration in material selection. Ceramics are inherently non ductile and may be prone to cracking under tensile or shear stresses. Fusion reactors systems may experience intense thermal and mechanical stresses, so toughness may be needed to ensure a robust design. Some ceramics such as Zirconia, Silicon Nitride and ceramic composite materials exhibit enhance toughness and may be selected for this reason.
- Radiation Effects: The intense neutron bombardment inside a fusion reactor can degrade the properties of all materials including ceramics over time. Ceramics could have reduced mechanical properties, lose their ability to withstand high temperatures, or even undergo dimensional changes.
- Limited Material Selection: Ceramic materials differ considerably and it’s important to consider the best combination of properties required such as, high-temperature resistance, thermal conductivity, electrical insulation, mechanical strength and radiation tolerance for the fusion application. There may need to be some compromises in finding the right balance of properties within a single ceramic material.
- Manufacturing limitations: Producing complex shapes and large sizes from ceramics can be difficult and expensive. This can limit their use in some applications within a fusion reactor.
Despite these limitations, researchers are actively developing new ceramic materials and improving fabrication techniques to overcome them. Here are some areas of focus:
- Developing tougher ceramics: Research is ongoing to create ceramics that are more resistant to cracking under stress, even at high temperatures.
- Understanding radiation effects: Scientists are studying how radiation affects different ceramics and developing methods to mitigate these effects.
- Novel fabrication techniques: New methods for shaping ceramics, such as additive manufacturing, are being explored to create complex shapes more easily and cost-effectively.
By understanding these limitations, ceramics have the potential to play a more significant role in future fusion reactors, close to the central fusion environment and for other peripheral components.
-
What materials are used in fusion reactors?
Fusion reactors require special materials that can withstand the incredibly harsh environment inside the reactor. Technical / advanced ceramics can provide the properties required to withstand these harsh environments. There are a combination of materials required in a reactor;
1. Structural materials form the main body of the reactor and need to be very strong and resistant to the intense heat and radiation. Some examples are steels modified to be less radioactive when bombarded by neutrons, copper, titanium, vanadium alloys and fiber-reinforced silicon carbide.
2. Plasma-facing materials line the inner wall of the reactor vessel and are in close proximity to the hot plasma. They need to be able to withstand high temperatures, particle bombardment, and chemical erosion.
3. Breeder blanket and heat exchange materials. Ceramics that are chemically inert and have good thermal properties include Shapal Hi M Soft, Macor, Alumina, Boron Nitride and Zirconia.
4. Magnetic confinement materials. Ceramics are suitable for cryogenic and high magnetic field applications.
5. Control, instrumentation and peripherals. Ceramics are likely to be incorporated in electrical, electronic and sensor control applications throughout the fusion systems.
The choice of materials for a fusion reactor is a complex one. The best materials will depend on the specific design and related challenges of the fusion reactor which can be very different from one another.