Material Properties
- High strength and high fracture toughness
- High hardness and wear resistance
- High density
- High temperature capability up to 2,400ºC
- Good frictional behaviour
- Non-magnetic
- Electrical insulation
- Low thermal conductivity
- Good chemical resistance
- Modulus of elasticity similar to steel
- Coefficient of thermal expansion similar to iron
Typical Applications
- Precision ball valve (balls and seats)
- Pump seals
- Valves and impellors
- High density grinding media
- Oxygen sensors
- Thread guides
- Fuel cell membranes
- Cutting blades
- Radio frequency heating susceptors
- Medical prostheses
- Metrology components
- Metal Forming
- Gears
- Bushes
- Bearings
- Drive Shafts
Zirconia (ZrO2) Component Manufacturing
Small batch production of zirconia does depend on the geometry of the component. There are three general processing routes:
- Precision grind a general blank of zirconia
- Laser cut a zirconia substrate
- Injection moulding
For higher quantities, Zirconia (ZrO2) lends itself to the injection moulding process rather well. Expensive tooling is required but a high degree of dimensional accuracy can be achieved.
Laser cutting zirconia is also a relatively straight forward process. The limits on thickness that a laser can go through is typically 1mm. Zirconia (ZrO2) in this form is widely used throughout the electronics industry.
Precision Ceramics has over 20 years’ experience of developing high-quality technical ceramic parts and components for applications in an ever-widening field of applications. Our highly-experienced team of engineers and operators combined with our in-depth ceramic material knowledge and ultra-precise machining centres allow us offer the most advanced technical ceramic solutions for our customers at the most competitive prices.
Related Topics
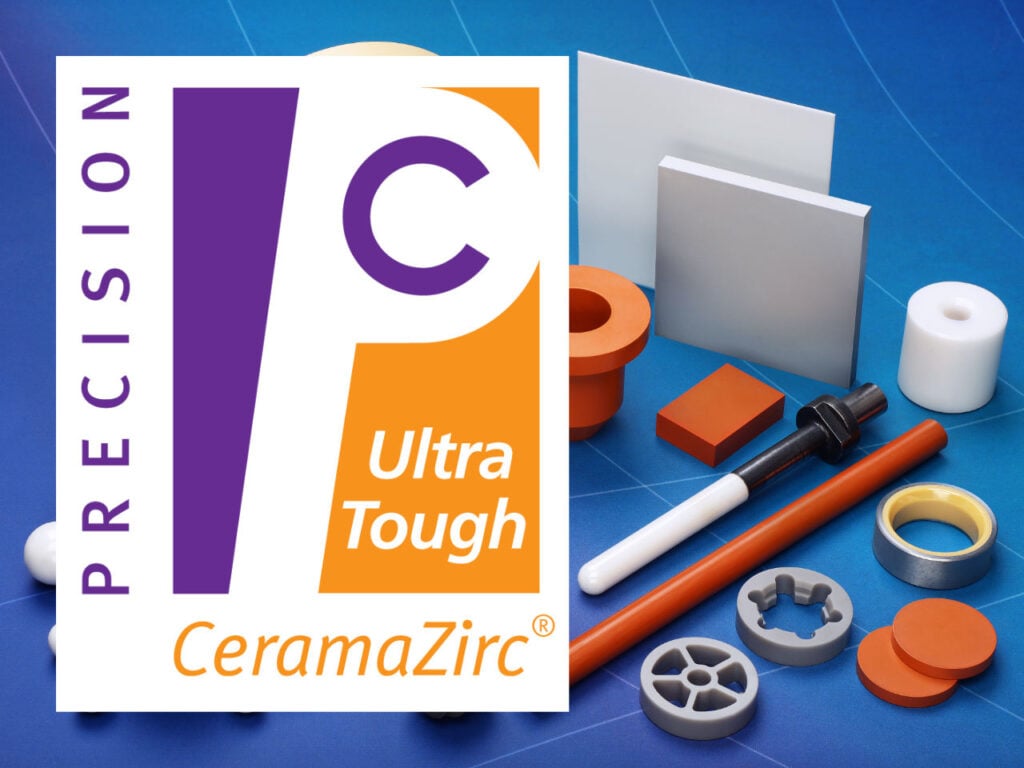
Zirconia
CeramaZirc™
Unlike traditional ceramics that tend to be hard and brittle, Zirconia offers high strength, wear resistance, and flexibility far beyond those of most other technical ceramics.
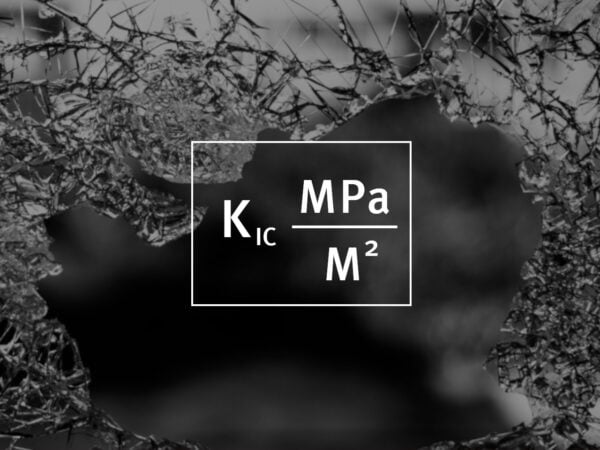
Fracture Toughness
The ability to resist fracture is a mechanical property of materials known as fracture toughness. For advanced ceramics it uses a critical stress intensity factor known as KIC where the fracture normally occurs at the crack terminations.