How do you choose a ceramic material for mechanically demanding applications?
Choosing the right ceramic for based on mechanical properties involves considering strength, toughness and hardness. These properties are distinct and actually mean different things. Strength measures a material’s ability to withstand loads, toughness looks at its resistance to cracks, and hardness focuses on resistance to scratches.
Some ceramics that perform well in terms of these properties include Zirconia (the toughest and strongest), Silicon Nitride (reasonably tough and strong):

Silicon Carbide (hard and strong), and Boron Carbide (even harder). Alumina, while not excelling in any one property, is a reliable and cost-effective all-round choice.

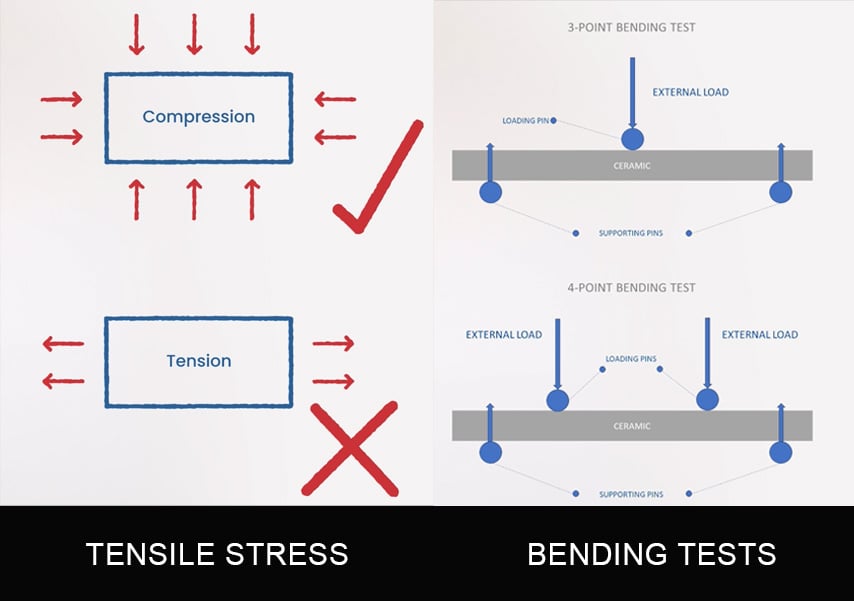
How do ceramics behave mechanically in fatigue, or under permanent tensile loads?

Young’s Modulus, which is a measure of stiffness, can be crucial for ceramic performance. Zirconia, for instance, has a stiffness similar to steel, making it springy in thin sections, whilst alumina and other engineering ceramics are twice as stiff.


How do temperature or the environment affect the mechanical properties?
In general, most ceramic materials exhibit lower strengths at higher temperatures due to the softening of any glassy grain boundary phase they may contain. However, this decrease is not linear and there’s usually an “upper use temperature” above which the material is considered unsafe for applications.
Some ceramics, especially zirconia, can be sensitive to moisture, which can accelerate crack growth. However, manufacturers are typically well-equipped to prevent this issue. Radiation can be a concern in specific applications, such as nuclear reactors or space environments, and different ceramic types have varying abilities to handle it, so its always a good idea to get expert advice where ceramics are needed for particularly demanding conditions.
Does the ceramic production route or component design affect the mechanical properties?
The manufacturing process used significantly influences the final properties of ceramics because it affects the material’s microstructure and the presence of defects.

Wet or soft processing methods like slip casting or injection moulding tend to create more defects compared to dry, powder-based approaches.
The shape, size and design of ceramic components also play a vital role in their properties. Sharp edges, tight corners and thin sections can act as crack initiators and should be avoided.

When this isn’t achievable, incorporating 0.2-0.5 mm edge chamfers or maximizing radii can help. Smaller and rounder parts generally exhibit greater strength and avoiding situations where ceramics see tensile properties is very important.

Andy Duncan & Precision Ceramics
Andy Duncan, Business Development Director at Precision Ceramics, has spent over 30 years in Engineering Ceramics within Technical Management and Business Development roles. Andy’s ceramics application experience is broad, spanning the design and selection of ceramic materials to metal joining, and piezoceramics. Combined with diverse application and design knowledge in various markets, Andy can help guide you towards the best-suited material for your application.
Precision Ceramics is a leader in supplying customized technical ceramics solutions. We go beyond mere manufacturing – we partner with you at every stage of material selection, product design, and development.
If you have any questions regarding which ceramic material might be best for your application, please don’t hesitate to contact us.
Related topics:
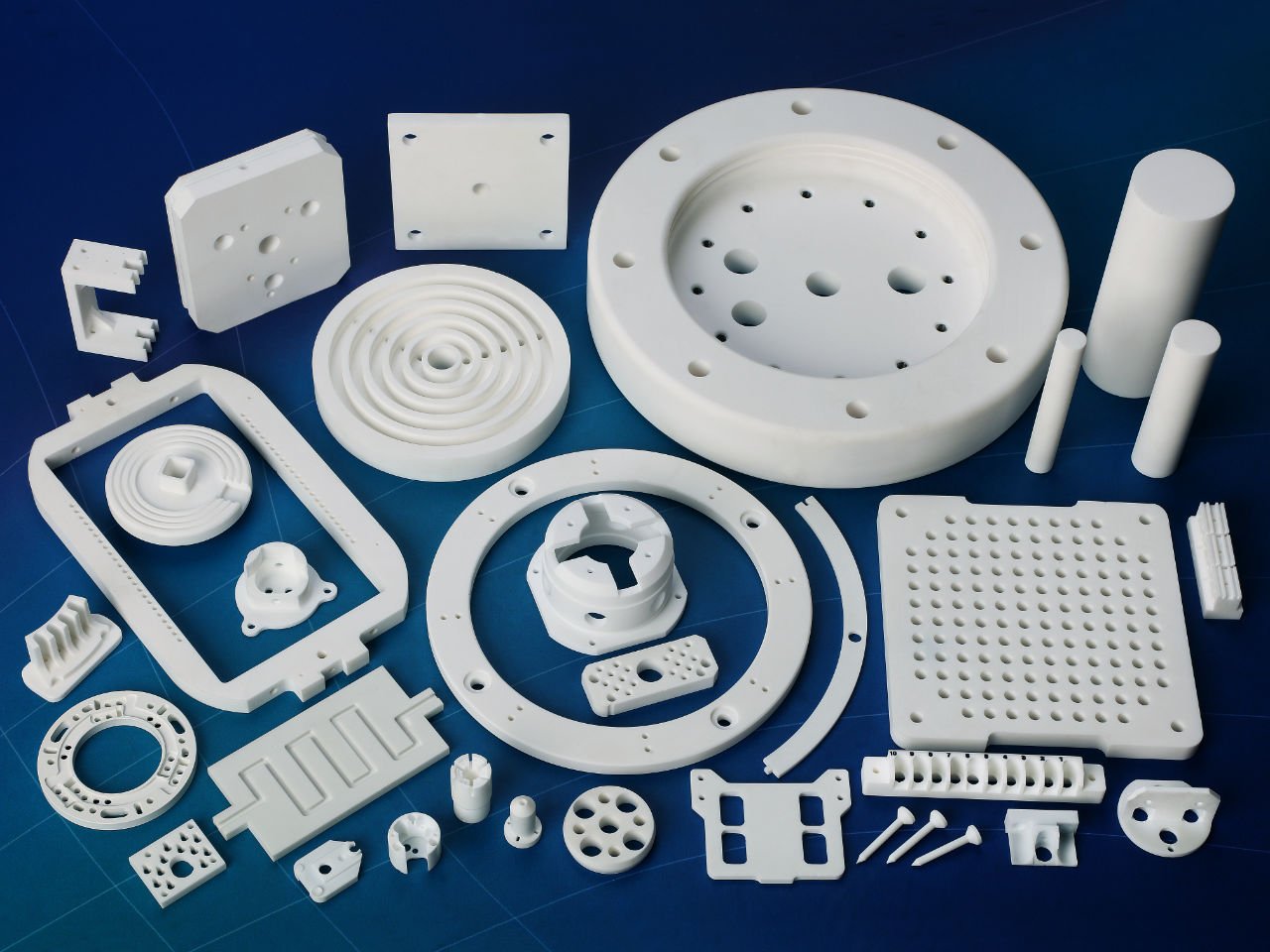
Materials
Precision Ceramics offers a wide range of advanced advanced ceramic materials to ensure that we have the right material for your application.
Ceramic Material Properties
View the mechanical, thermal, and electrical properties to identify which materials best suit your application based on their characteristics.