NSU Motorenwerke AG, a well-established German manufacturer of automobiles, motorcycles and pedal cycles and more commonly known simply as NSU, subsequently licensed the design of the Wankel engine to many companies around the world and whilst the basic design concept of the engine has remained steadfastly the same, many improvements have been made over the years. The Wankel engine has the unique advantages of compact size, high performance, relative simplicity, low weight and reliability over the most commonly used internal combustion engine employing reciprocating pistons. Nowadays the engine is used in a wide variety of applications including cars, motorcycles, racing cars, aircraft, go-karts, jet skis, snowmobiles, chain saws, and auxiliary power units. Whilst the design of the engine has enjoyed unprecedented success, one common problem has been the seals between the rotor and housing most commonly known as ‘tip’ or ‘apex’ seals. These have a tendency to wear against the rotor housing and over a period of time can distort causing a loss in compression and decrease in performance. In extreme cases, this distortion can stop the engine working altogether.
The Perfect Tip
One solution to this problem has been to install ceramic tip seals manufactured from a special type of silicon nitride. The seals – designed and manufactured by Precision Ceramics – provide an added degree of hardness and toughness over conventional steel seals which extends the operating life of the engine and reduces maintenance costs and downtime.
Unlike conventional steel seals, ceramic tip seals are dimensionally stable through all temperature ranges. They are manufactured to such high tolerances that the wear-in time is virtually negligible. Additionally, the seals have an almost perfect surface finish which promotes a better and longer lasting seal between the rotor and the housing.

Interested in finding out more and if any of our materials are the right fit for your application? Please don’t hesitate to get in touch.
Related topics:

Silicon Nitride
CeramaSil-N™
Silicon Nitride has the most versatile combination of mechanical, thermal, and electrical properties of any technical ceramic material.
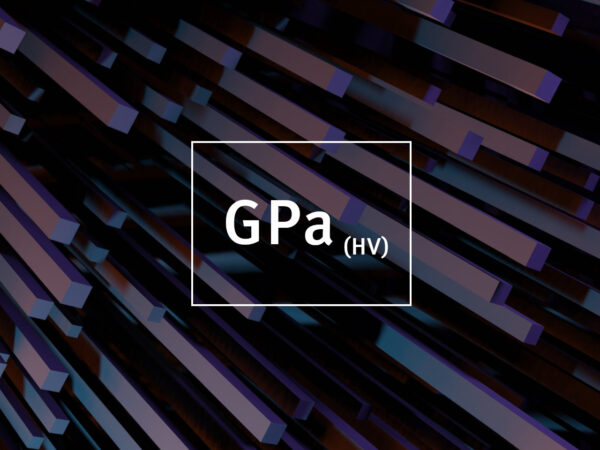
Hardness
One of the most valuable characteristics of advanced ceramics in high-performance applications is their extreme hardness. Hard ceramic materials are used for a wide range of applications in diverse fields and applications such as cutting tools for milling and grinding.