Ceramic Materials Overview
Technical ceramic materials have the ability to make products lighter, more efficient, longer lasting, reduce maintenance intervals, and reduce operating costs. They are frequently being used to replace metals, polymers, and refractory materials in a wide variety of applications due to their notable high temperature capability, hardness, and electrical properties.
Precision Ceramics offers a wide range of advanced technical ceramic materials to ensure that we have the right material for your application.
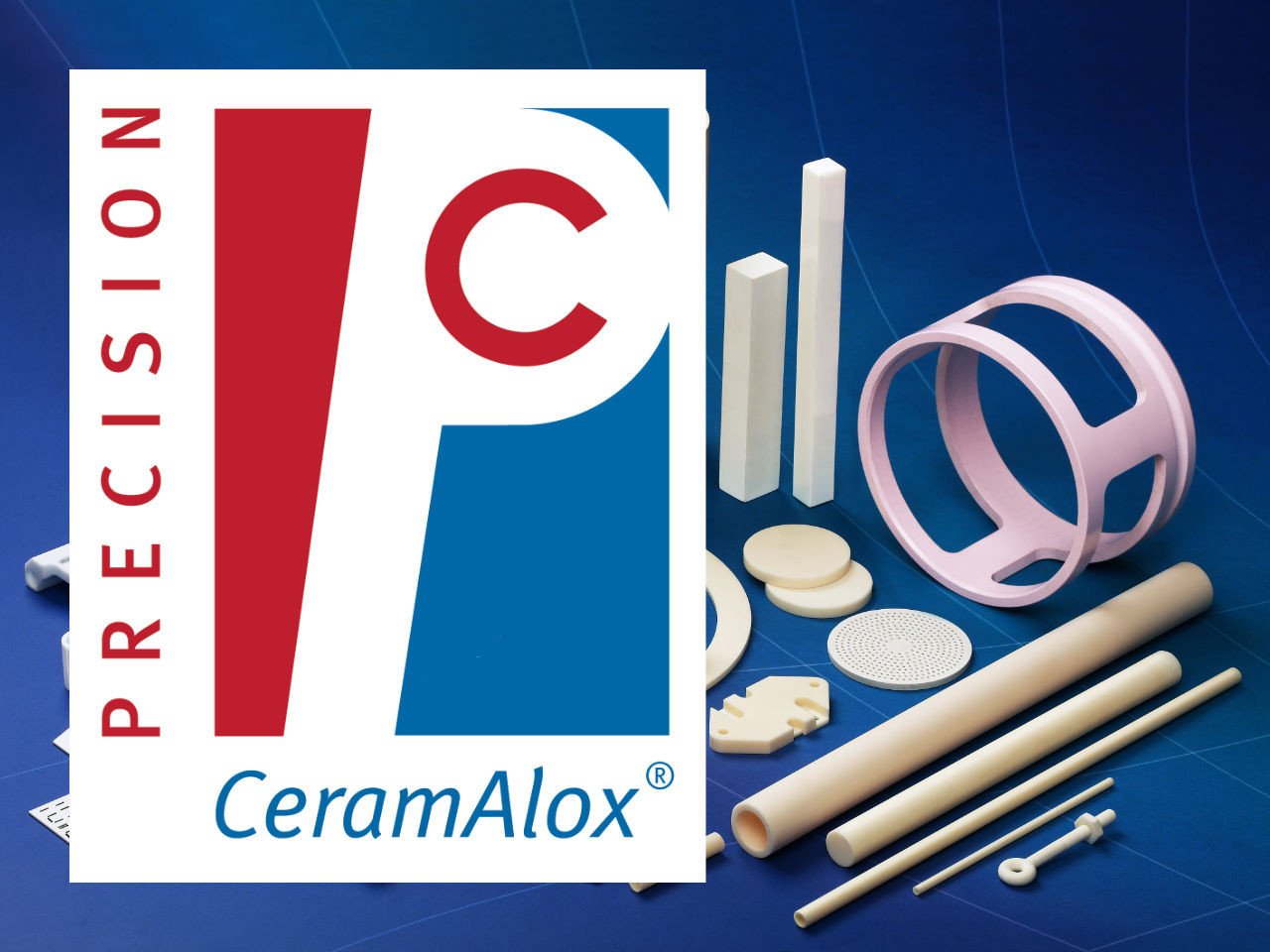
Alumina (Aluminium Oxide)
CeramAlox™
Alumina, also known as Aluminium Oxide, is a hard wearing advanced technical ceramic material frequently used in a wide variety of industrial applications.
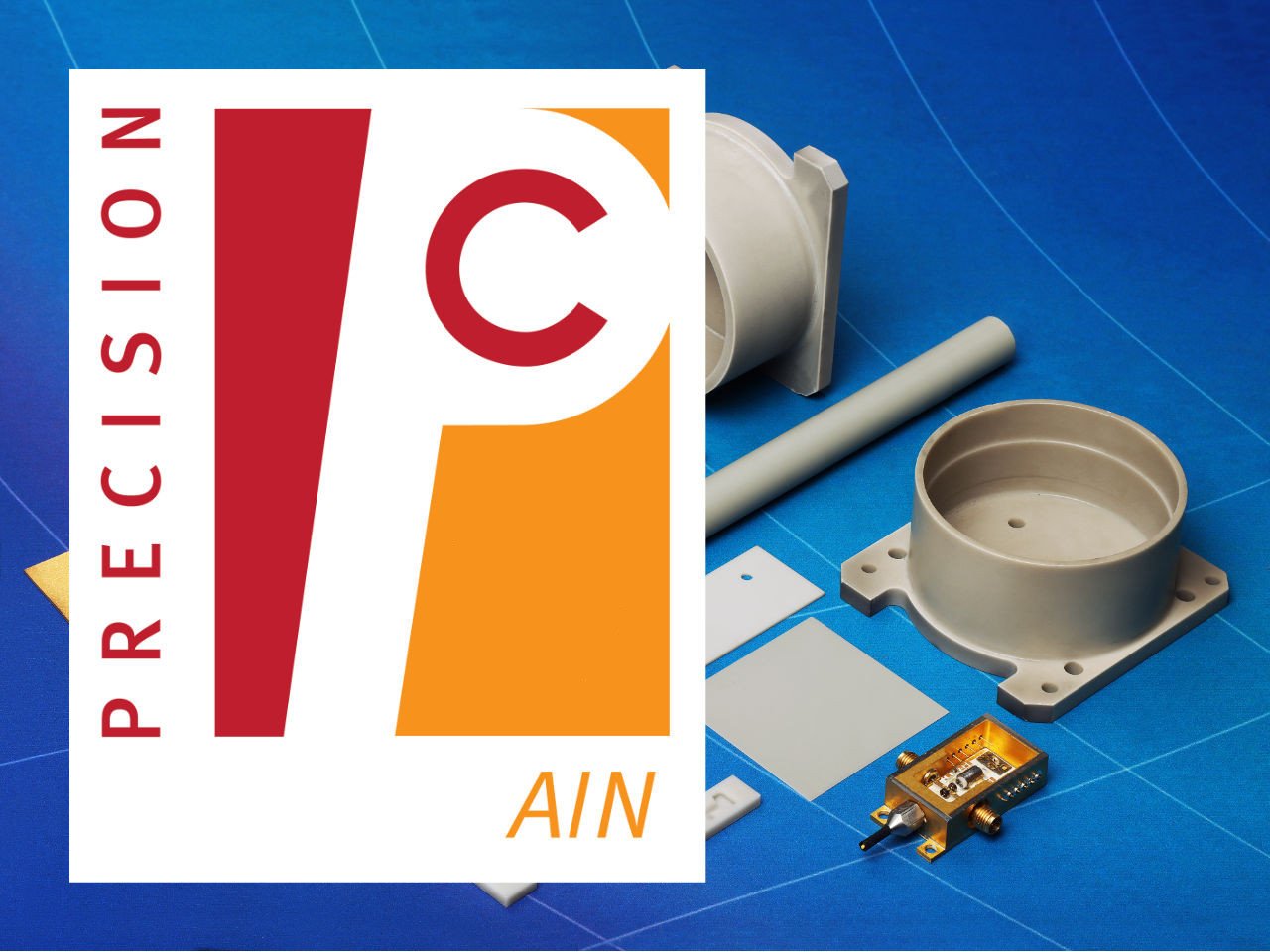
Aluminum Nitride
CeramAlum™
Aluminum Nitride (AlN) is an excellent material to use if high thermal conductivity and electrical insulation properties are required -- an ideal material for use in thermal management and electrical applications.
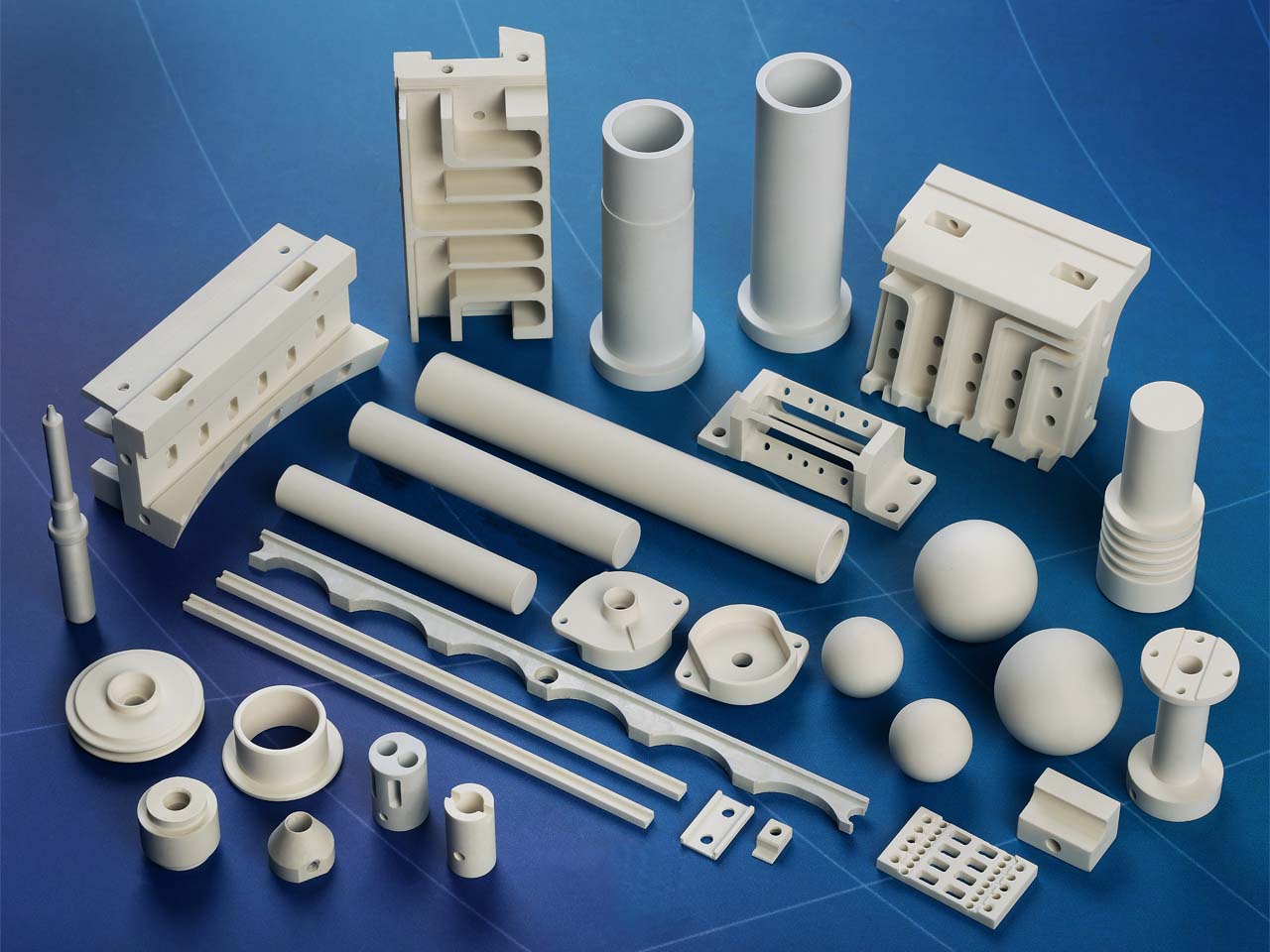
Shapal Hi M Soft™
Machinable AlN
Shapal Hi M Soft is a hybrid type of machinable Aluminum Nitride (AlN) ceramic that offers high mechanical strength, electrical insulation, and thermal conductivity.
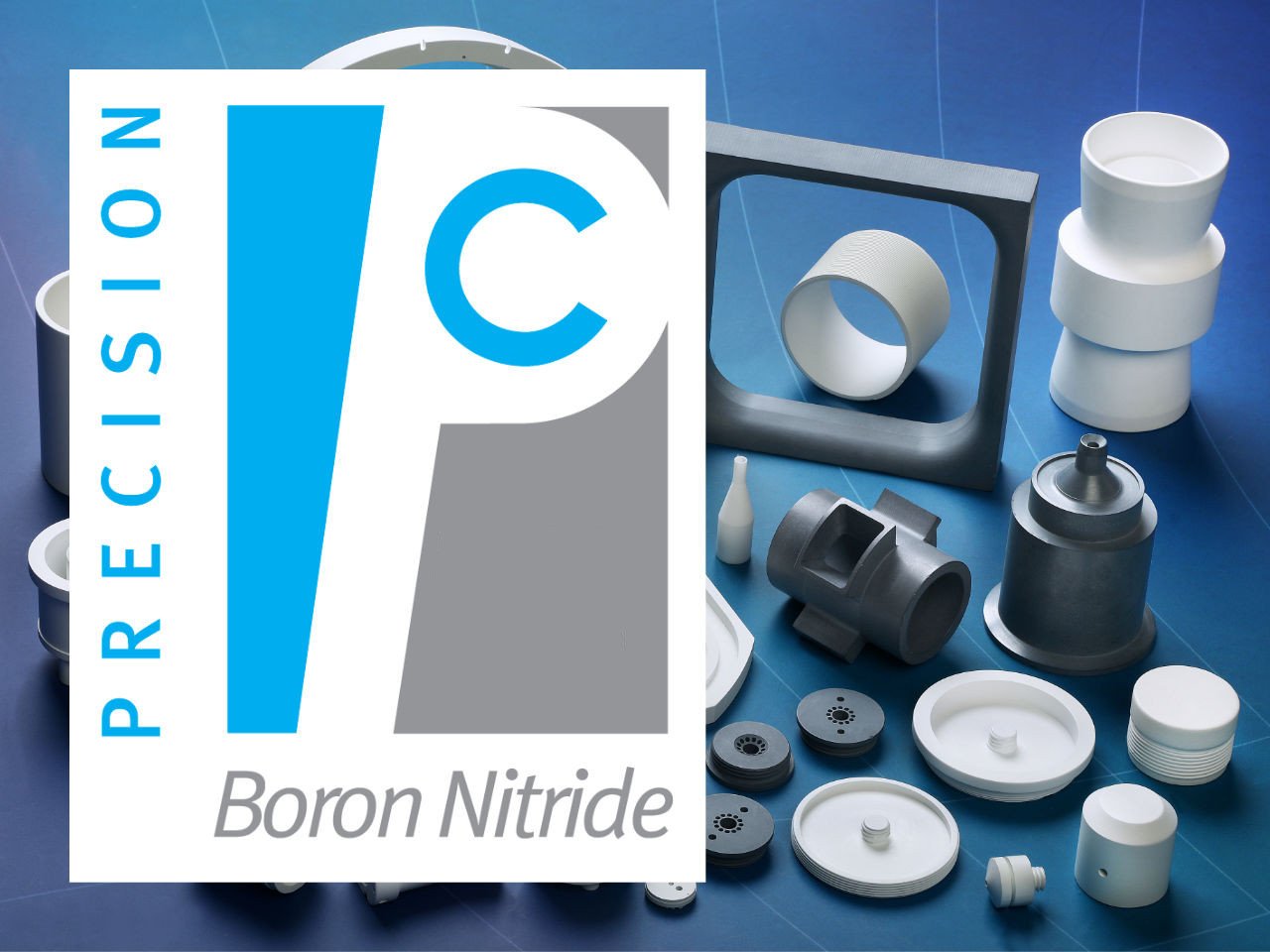
Boron Nitride
Boron Nitride Grades
Boron Nitride (BN) is an advanced synthetic ceramic material available in solid and powder form. It has outstanding thermal conductivity, electrical insulation and thermal properties and is easy to machine.
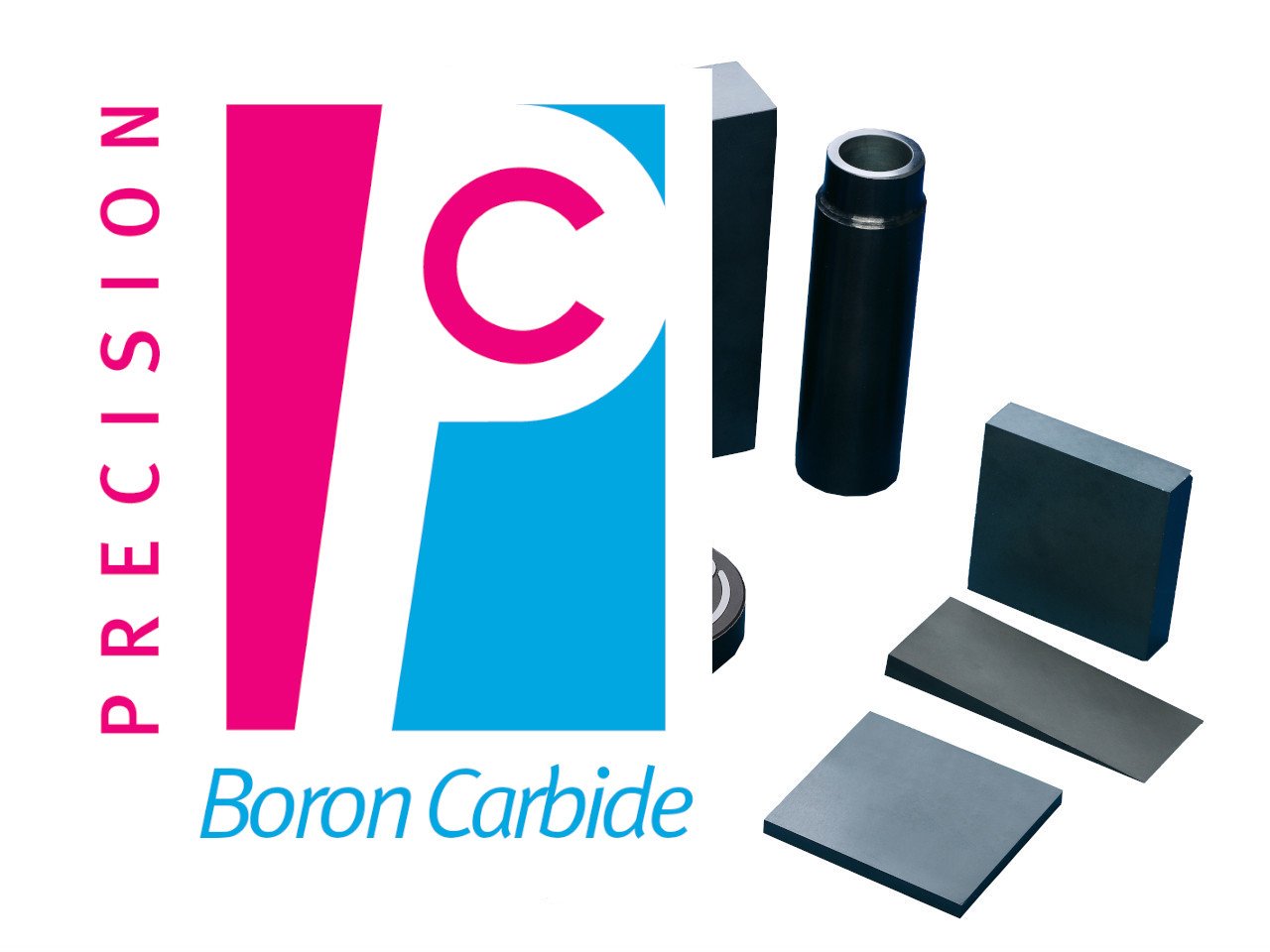
Boron Carbide
DuraShock™ & DuraWear™
Boron Carbide (B4C), also known as black diamond, is the third hardest material after diamond and cubic boron nitride. It is a suitable material for many high performance applications due to its attractive combination of properties.
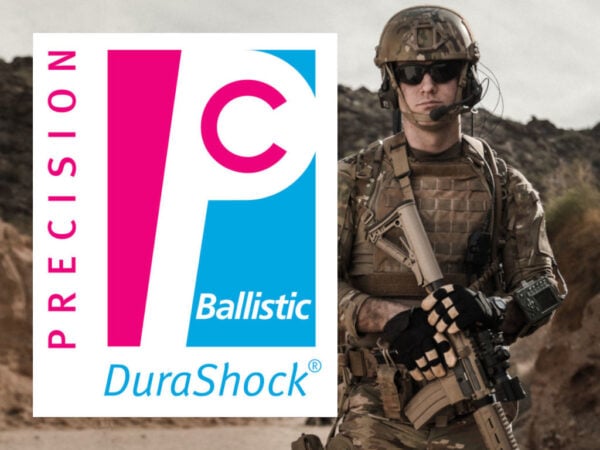
Boron Carbide / Silicon Carbide
DuraShock™
DuraShock is a Boron Carbide / Silicon Carbide ceramic composite, developed to give the very best combination of high ballistic performance and weight saving considerations.
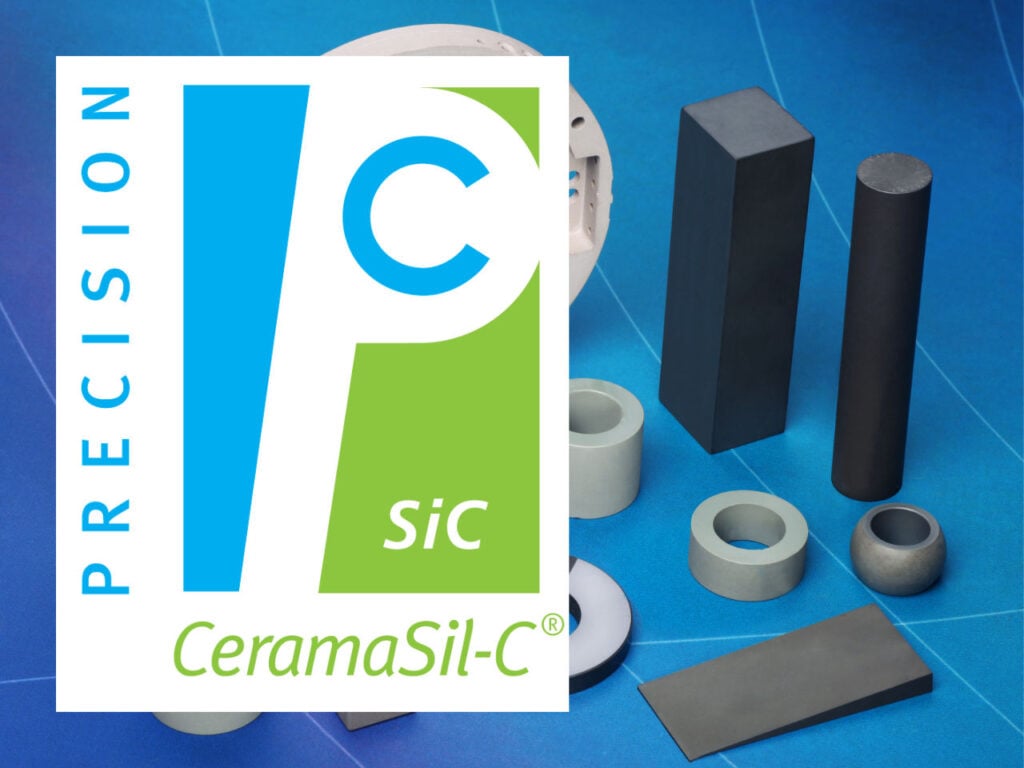
Silicon Carbide
CeramaSil-C™
Silicon Carbide (SiC) is one of the lightest, hardest, and strongest technical ceramic materials with exceptional thermal conductivity, acid resistance, and low thermal expansion.

Silicon Nitride
CeramaSil-N™
Silicon Nitride has the most versatile combination of mechanical, thermal, and electrical properties of any technical ceramic material.
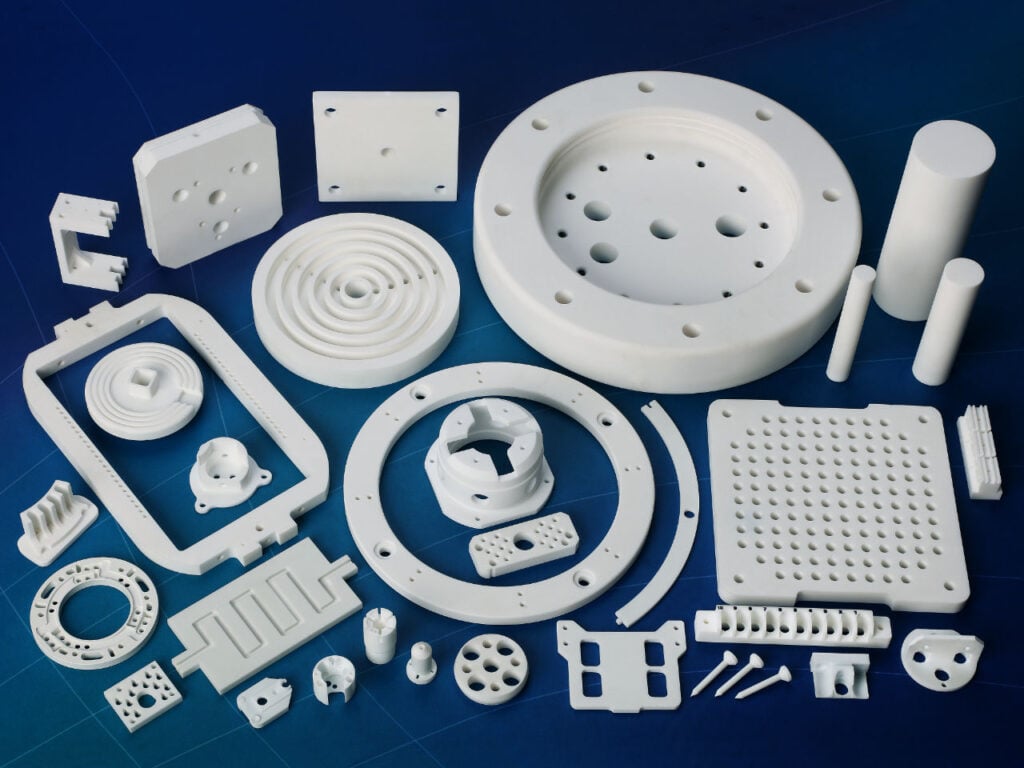
Macor®
Machinable Glass Ceramic
Macor is a hybrid glass-ceramic with the machinability of a metal, and the performance of an advanced technical ceramic. Macor is an excellent thermal and electrical insulator.
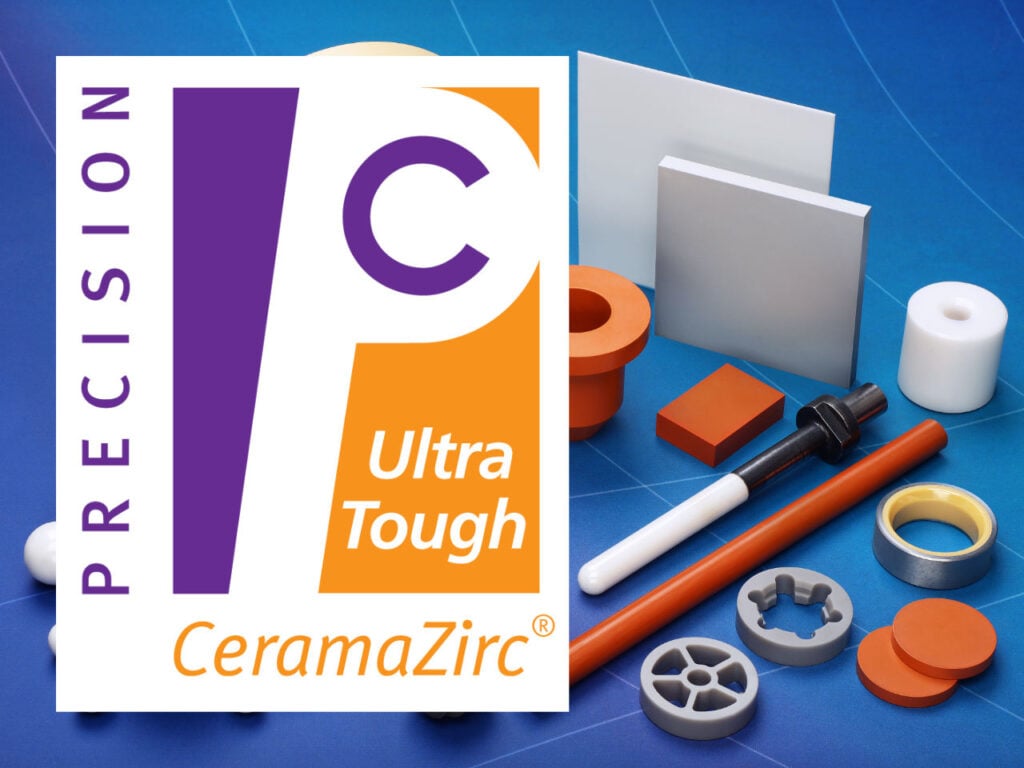
Zirconia
CeramaZirc™
Unlike traditional ceramics that tend to be hard and brittle, Zirconia offers high strength, wear resistance, and flexibility far beyond those of most other technical ceramics.

Zirconia Toughened Alumina
CeramAlloy™
Zirconia Toughened Alumina (ZTA) is a high performance ceramic composite and a unique ceramic material by way of exhibiting a combination of high hardness, strength, wear and corrosion resistance.

Alumina Toughened Zirconia
CeramAlloy™ ATZ
Alumina Toughened Zirconia (ATZ) is a high performance ceramic composite and a unique ceramic material by way of exhibiting a combination of high hardness, strength, wear and corrosion resistance characteristics to their Alumina component.
Need help?
Not sure which ceramic material is right for your application? Learn more about technical ceramics, check out our ceramic materials comparison chart, or contact us and we’ll be more than happy to help out.
Frequently Asked Questions
-
What are technical ceramics?
Ceramics, defined by the broad definition of “inorganic solids”, are one of the main classes of materials, along with metals, polymers, and composites. There are several different types of ceramics, with technical ceramics (also known as engineered ceramics or advanced ceramics) being the group with the highest performing mechanical, electrical, and/or thermal properties. Their high performance is due in part to their extremely high purities which are most commonly metal compounds combined with oxides, carbides, or nitrides. Ceramics have the ability to increase product lifespan, increase efficiency, reduce overall maintenance costs, and improve performance.
-
What are the advantages of technical ceramics?
High Hardness
One of the most common properties of engineered ceramics is extreme hardness (& stiffness) – some are more than 4 times harder than stainless steel. This high hardness directly translates into excellent wear resistance, meaning that many technical ceramics have the ability to keep their precise, high-tolerance finish much longer than any other material.
Extreme Compressive Strength
Technical ceramics have very high strength, however, this is only when compressed. For example, many technical ceramics can withstand extremely high loads ranging from 1000 to 4000 MPa. Titanium on the other hand, which is regarded as a very strong metal, only has 1000 MPa of compressional strength.
Low Density
Another common property of technical ceramics is their low density, ranging from 2 to 6 g/cc. This is significantly lighter than stainless steel (8 g/cc) and titanium (4.5 g/cc) with only the much softer aluminum being similar in density. Due to their high hardness and low weight, technical ceramics are increasingly being used in a variety of industries in applications where no other material can match their performance & long life.
Excellent Wear Resistance
Many technical ceramics are able to withstand incredibly high temperatures while still retaining their mechanical & electrical properties. Where all metals and polymers will start to compromise their properties, technical ceramics will continue to function with consistent performance and reliability. This property makes ceramics appropriate for use in very high temperature applications like furnaces, jet engines, brake systems, and cutting tools.
Excellent Electrical Properties
Technical ceramics tend to be excellent electric insulators (high dielectric strength). They are especially useful in high-temperature applications where other materials’ mechanical & thermal properties tend to degrade. Some ceramics have low electrical loss & high dielectric permittivity; these are typically used in electronic applications like capacitors and resonators. Additionally, the ability to combine an insulator with a structural component has lead to many product innovations.
Ultra-High-Temperature Ability
Technical ceramics can function in situations where no metal (or nearly any other material) can maintain their properties. Some ceramics can operate in temperatures in excess of 1750°C, putting them in a class of their own as ultra-high-temperature materials. These ceramics have proven to be invaluable in high-temperature applications like engines, turbines, & bearings where they have increased the lifespan, performance, and efficiency.
Thermally Conductive or Insulative
Different types of technical ceramic materials have wildly varying thermal properties. There are some ceramics (Aluminum Nitride) that are highly thermally conductive and are commonly used as heat-sinks or exchangers in many electrical applications. Other ceramics are much less thermally conductive, making them suitable for a wide range of applications.
Chemically Inert & Corrosion Resistant
Technical Ceramics are very chemically stable and have low chemical solubility, making them highly resistant to corrosion. Metals and polymers cannot offer the same inertness or corrosion resistance, making ceramics a highly attractive option in many commercial and industrial applications, particularly when wear resistance is also needed.
-
What are the drawbacks of technical ceramics?
Poor Shear & Tensile Strength
With all of these advantageous properties, you may be wondering why we do not see technical ceramics more frequently. This is due to a variety of reasons, but mostly because other types of strength are tensile and shear; this is where technical ceramics strength can be 15 times less than those of metals.
High Brittleness
Another issue that can arise with technical ceramics is that they can be very brittle due to their low ductility. This means that technical ceramics have very poor impact resistance. This property is caused by technical ceramics unique atomic bonds. Metals have “metallic” bonds which are relatively low strength, however, they can bond with atoms in any direction. This ability to have many multi-directional bonds is what makes metals ductile, tough, and relatively strong. Ceramics obviously do not have metallic bonds, instead they have ionic and covalent bonds – these are very strong, however they can only bond in very specific directions. This highly organized bonding structure means that it is difficult for the atomic structure to shift, making ceramics not malleable.
Difficult to Design
Every type of technical ceramic has specific thermal, mechanical, and electrical properties that can vary dramatically depending on the operating conditions & product design. In fact, even the manufacturing process of the exact same type of technical ceramic material can drastically change its properties.
-
Do you supply or work with other materials that are not listed on your website?
Precision Ceramics is unusual as we offer the full range of technical ceramics from machinable grades like Macor and Shapal through to materials that require diamond grinding like alumina, zirconia, carbides and nitrides. We can machine and supply virtually any ceramic material – please contact us with your specific requirements for more information. Our goal it to optimize the material selection and design for the customer, rather than what is right for our capability.
-
Can you help me with material selection and design of ceramics?
Yes we can. We have a competent team of technical sales staff with many years’ experience that can help you chose the right material. Whether it is for wear, thermal management, electrical properties, or something else, we can help you by designing an appropriate component for ceramic manufacture from simple suggestions to more complex solutions. Contact us with details of your application and one of our engineers will be happy to help you.