Zirconia Toughened Alumina (Zr-Al2O3) – CeramAlloy™
Material Advantages
- High performance Zirconia Toughened Alumina ceramic composite
- Use temperatures up to 1,500°C
- Chemical inertness
- Excellent wear resistance
- High bending strength
- High fracture toughness
- Excellent balance between bending strength, hardness and fracture toughness
- Sintered to near theoretical density or Hot Isostatic Pressed for enhanced reliability
- Increased tolerance to hydrothermal aging
Applications
- Rollers and guides for metal forming
- Thread and wire guides
- Metal extrusion dies
- Deep well down-hole valves and seats
- High pressure equipment – ball valve balls and seats particularly suitable for high flow/abrasive fluids
- Focusing nozzles for abrasive media
- Ultra high pressure pumping elements
- Shaft bearings/bushings
Material Grades
We have produced two variations of Zirconia Toughened Alumina which are CeramAlloy ZTA and CeramAlloy Ultra Hard. The differing methods used to produce these materials resulted in slightly different properties and characteristics. We evaluate the similarities, differences, and properties of each material and its applications on this page.
CeramAlloy ZTA
General Properties
CeramAlloy ZTA is a high performance ceramic composite and a unique ceramic material by way of exhibiting a combination of high hardness, strength, wear and corrosion resistance resulting from its Alumina content, while still maintaining reasonably high fracture toughness resulting from its Zirconia content.
Applications
- High pressure equipment – ball valve balls and seats
- Rollers and guides for metal forming
- Thread and wire guides
- Deep well down-hole valves and seats
- Shaft bearings/bushings
CeramAlloy Ultra Hard
General Properties
CeramAlloy Ultra Hard is a high performance ceramic composite and a unique ceramic material by way of exhibiting a combination of high hardness, strength, wear and corrosion resistance resulting from its Alumina content, while still maintaining reasonably high fracture toughness resulting from its Zirconia content.
Applications
- High pressure equipment – ball valve balls and seats – particularly suitable for high flow/abrasive fluids
- Focusing nozzles for abrasive media
- Ultra high pressure pumping elements
- Deep well down-hole valves and seats
- Rollers and guides for metal forming
- Thread and wire guides
- Metal extrusion dies
Material Properties
General Properties
Property | Units | CeramAlloy ZTA | CeramAlloy Ultra Hard |
---|---|---|---|
Composition | – | Alumina/Zirconia | Alumina/Zirconia |
Color | – | White | Off White |
Mechanical Properties
Property | Units | CeramAlloy ZTA | CeramAlloy Ultra Hard |
---|---|---|---|
Density | g/cm3 | 4.1 | 4.18 |
Young’s Modulus | GPa | 335 | 350 |
Fracture Toughness | MPa x m1/2 | 7 | 5 |
Poisson’s Ratio | – | 0.23 | 0.22 |
Compressive Strength | MPa | 2500 | 3000 |
Flexural Strength | MPa | 600 | 850 |
Hardness (Vickers 500g) | GPa | 16 | 21.5 |
Thermal Properties
Property | Units | CeramAlloy ZTA | CeramAlloy Ultra Hard |
---|---|---|---|
Max Use Temp | °C | 1500 | 1500 |
Coefficient of Expansion 1 | 10-6/°C | 7 | 7.5 |
Thermal Conductivity @ 25°C | W/mK | 20 | 20 |
Thermal Shock Resistance ΔT | °C | 200 | 200 |
1 Coefficient of Thermal Expansion (CTE) describes how the size of an object changes with a change in temperature.
Electrical Properties
Property | Units | CeramAlloy ZTA | CeramAlloy Ultra Hard |
---|---|---|---|
Dielectric Strength DC @25°C | kV/mm | 16 | 16 |
Volume Resistivity @ 25°C | Ω cm | >1016 | >1016 |
Disclaimer: The values presented are mean and typical of those resulted from test samples. They are provided as an indication only to serve as guidance in the design of ceramic components and are not guaranteed in any way. The actual values can vary according to the shape and size of the envisioned component.
Datasheets
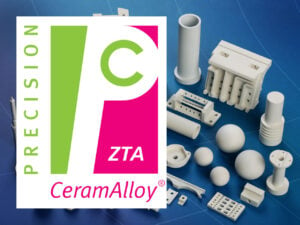
Zirconia Toughened Alumina
CeramAlloy ZTA
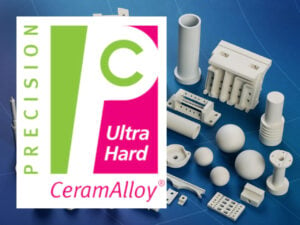
Zirconia Toughened Alumina
CeramAlloy Ultra Hard
CeramAlloy Material Machining
CeramAlloy can be machined in green, biscuit, or fully dense states. While in the green or biscuit form, it can be machined relatively easily into complex geometries. However, the sintering process that is required to fully densify the material causes the CeramAlloy body to shrink approximately 20%. This shrinkage means that it is impossible to hold very tight tolerances when machining the CeramAlloy pre-sintering.
In order to achieve very tight tolerances, fully sintered material must be machined/ground with diamond tools. In this process, a very precise diamond coated tool/wheel is used to abrade away the material until the desired form is created. Due to the inherit toughness and hardness of the material, this can be a time-consuming and costly process.
Precision Ceramics is your machining specialist for your advanced ceramic prototyping & manufacturing needs. We use our many years of technical ceramics experience to provide advice on materials, designs, and applications. If you would like to buy CeramAlloy plates, rods, tubes, or custom machined components, please contact us and one of our experts will be happy to assist you.
CeramAlloy Ultra Hard Video
In this short demonstration video, we compare the wear characteristics of Alumina and CeramAlloy Ultra Hard by using a sandblaster to erode a hole in the ceramic plates.
After 15 minutes of sandblasting, it is clear from the results that CeramAlloy Ultra Hard is the better choice for applications of extreme wear, but also where a high resistance to fracture is also required.
Frequently Asked Questions
-
What can Zirconia Toughened Alumina ceramic (CeramAlloy) be used for?
- Wire forming/drawing dies
- Insulating rings in thermal processes
- Precision shafts and axles in high wear environments
- Wear resistance pads
- Sandblasting nozzles
- Refractory material
- Extrusion dies
- Bushings and caps
- Fiber optic ferrules and sleeves
- Bearings & rollers
- Welding nozzles & pins
- Laser parts
- Electric insulator
- Ceramic guiders
- Medical and surgical component
- Mechanical seals
- Pumps, pistons, and liners
-
What's the difference between Zirconia, Alumina, and Zirconia Toughened Alumina (CeramAlloy)?
While Zirconia has the highest fracture toughness of all the oxide monolith ceramic materials, Alumina is one of the most cost effective ceramic materials yet exhibiting very high hardness, thermal stability and favourable electrical properties. CeramAlloy ZTA is a composite material based on Alumina and Zirconia and therefore combining to a certain extent the favourable properties of the two main constituents. So CeramAlloy ZTA will retain the very high hardness of Alumina but also show an increase in fracture toughness and bending strength owing to its Zirconia component so a true “best of both worlds”.
-
What are the properties of Zirconia Toughened Alumina (CeramAlloy)?
The following are some general properties of CeramAlloy ZTA ceramic.
- High density – up to 4.1 g/cm^3
- High flexural strength and hardness
- Good fracture toughness – moderate impact resistant
- High maximum use temperature
- Wear resistant
- Good frictional behaviour- favourable coefficient of friction
- Electrical insulator
- Corrosion resistance in acids and alkalis
-
What is Zirconia Toughened Alumina ceramic (CeramAlloy)?
CeramAlloy ZTA is a composite material based on Alumina and Zirconia and therefore combining to a certain extent the favourable properties of the two main constituents.