What is Flexural Strength?
Flexural strength, also known as bending strength, modulus of rupture, or transverse rupture strength, is the maximum stress that a material can withstand before failing in a bending test.
Advanced ceramics exhibit a range of flexural strengths depending on the ceramic material tested. The range is broad and materials based on Zirconia, ATZ or Silicon Nitride compositions exhibit relatively high bending strengths. Unlike metals, which deform before breaking, ceramics are purely elastic in nature and will fracture upon reaching their maximum yield.
Why is Flexural Strength Important?
Materials with high flexural strength are essential for high-performance applications in industries like aerospace, medical implants, and automotive engineering.
Precision Ceramics Alumina Toughened Zirconia (ATZ) is a leading option, offering exceptional flexural strength of up to 1,800 MPa. A high flexural strength may be required to support application stresses that arise from mechanical or thermal factors for example.
In this video, Andy Duncan explores why overdesigning for both short and long-term loads is crucial when working with ceramics. Understanding the principles covered in this video can help you make smarter material choices if you’re working with ceramics in engineering or design.
Materials Ranked by Flexural Strength
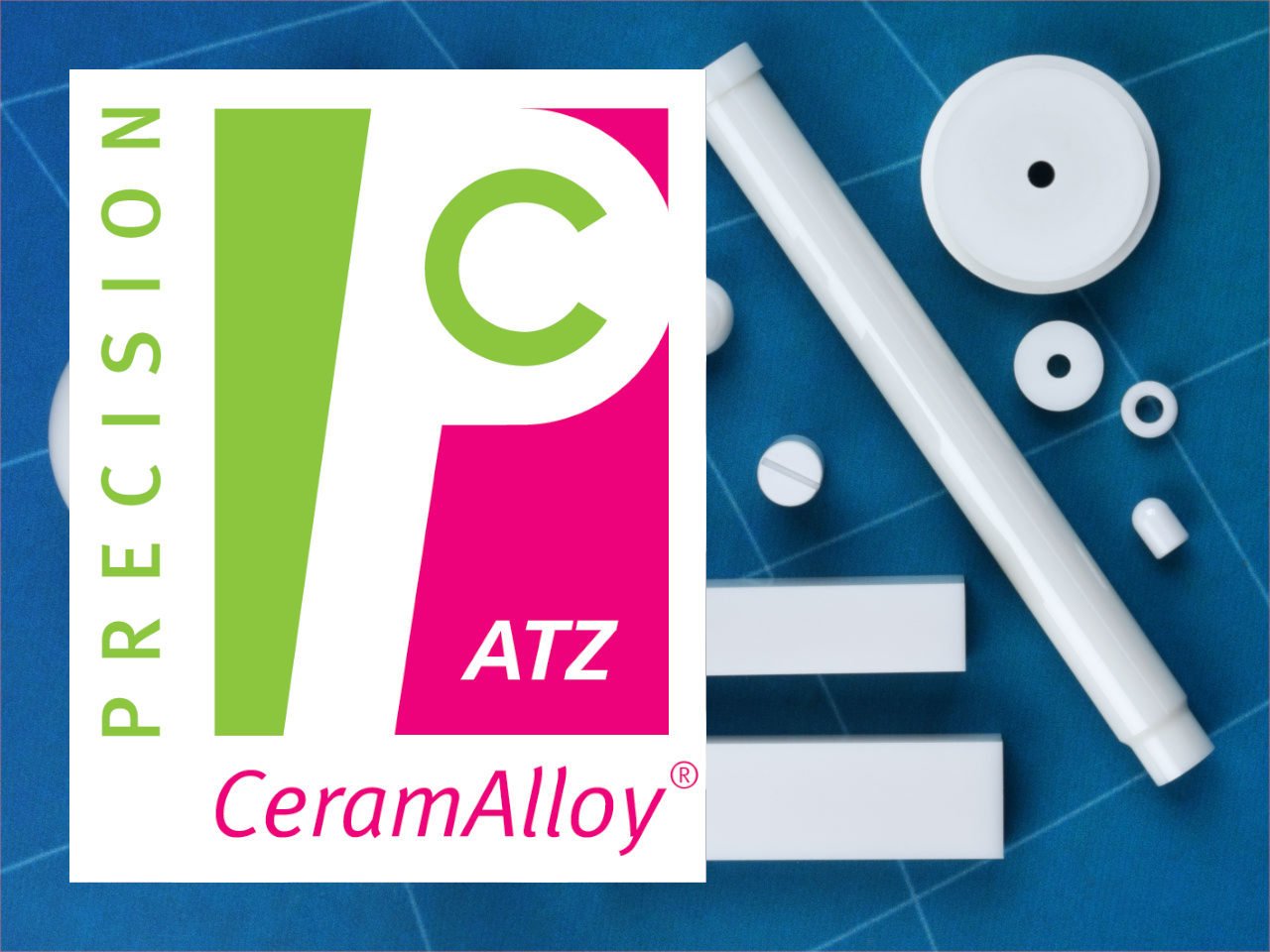
Alumina-Zirconia (ATZ) - CeramAlloy ATZ™
- Flexural Strength: 1800 MPa
- Key Features: High hardness, superior wear and corrosion resistance, and excellent fracture toughness.
- Best For: High-stress applications requiring durability and reliability.
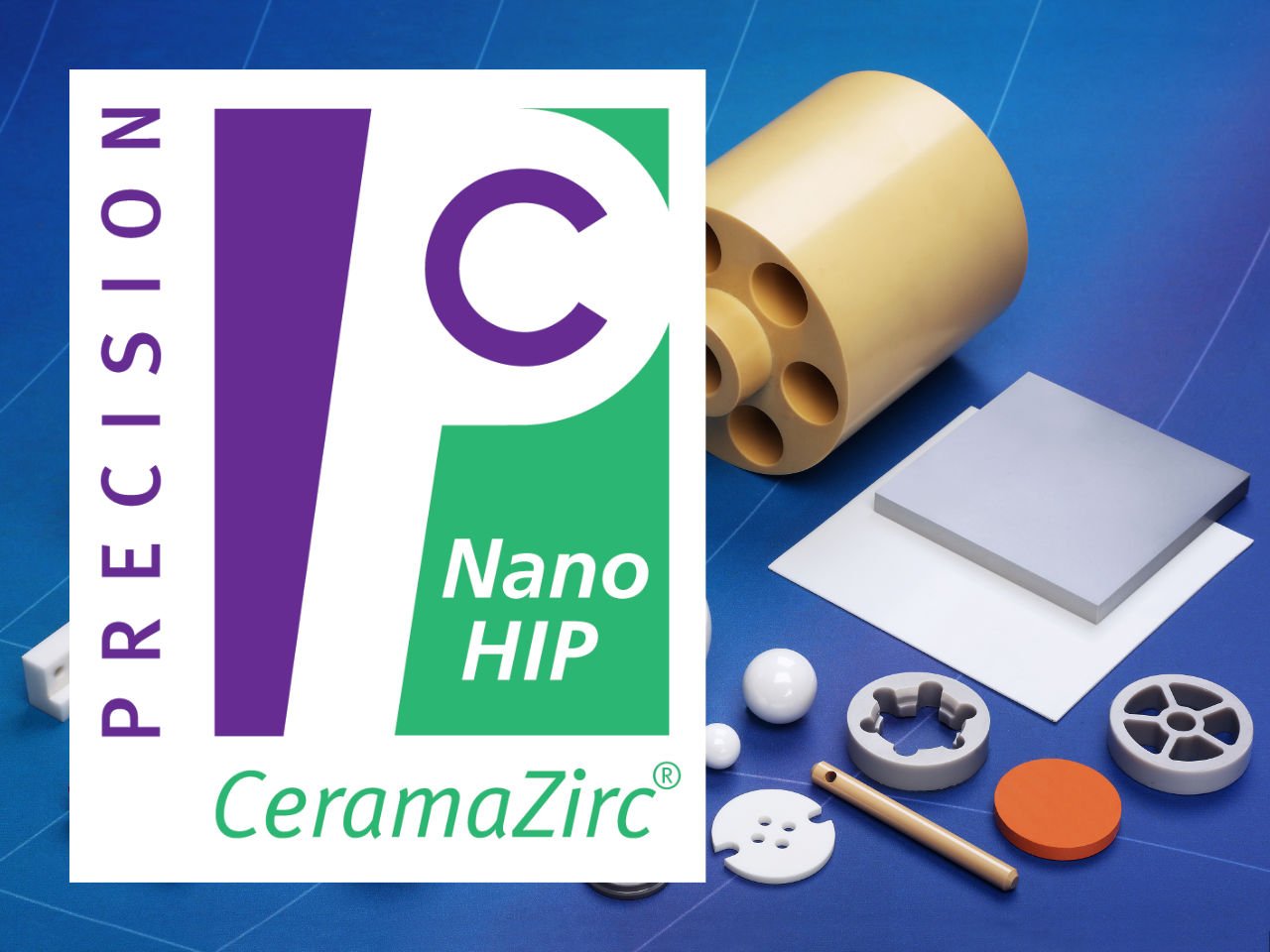
Zirconia (ZrO2) - CeramaZirc™ Nano HIP
- Flexural Strength: 1400 MPa
- Key Features: Nano-grade powder composition, high strength, and outstanding wear resistance.
- Best For: Applications demanding superior mechanical performance.
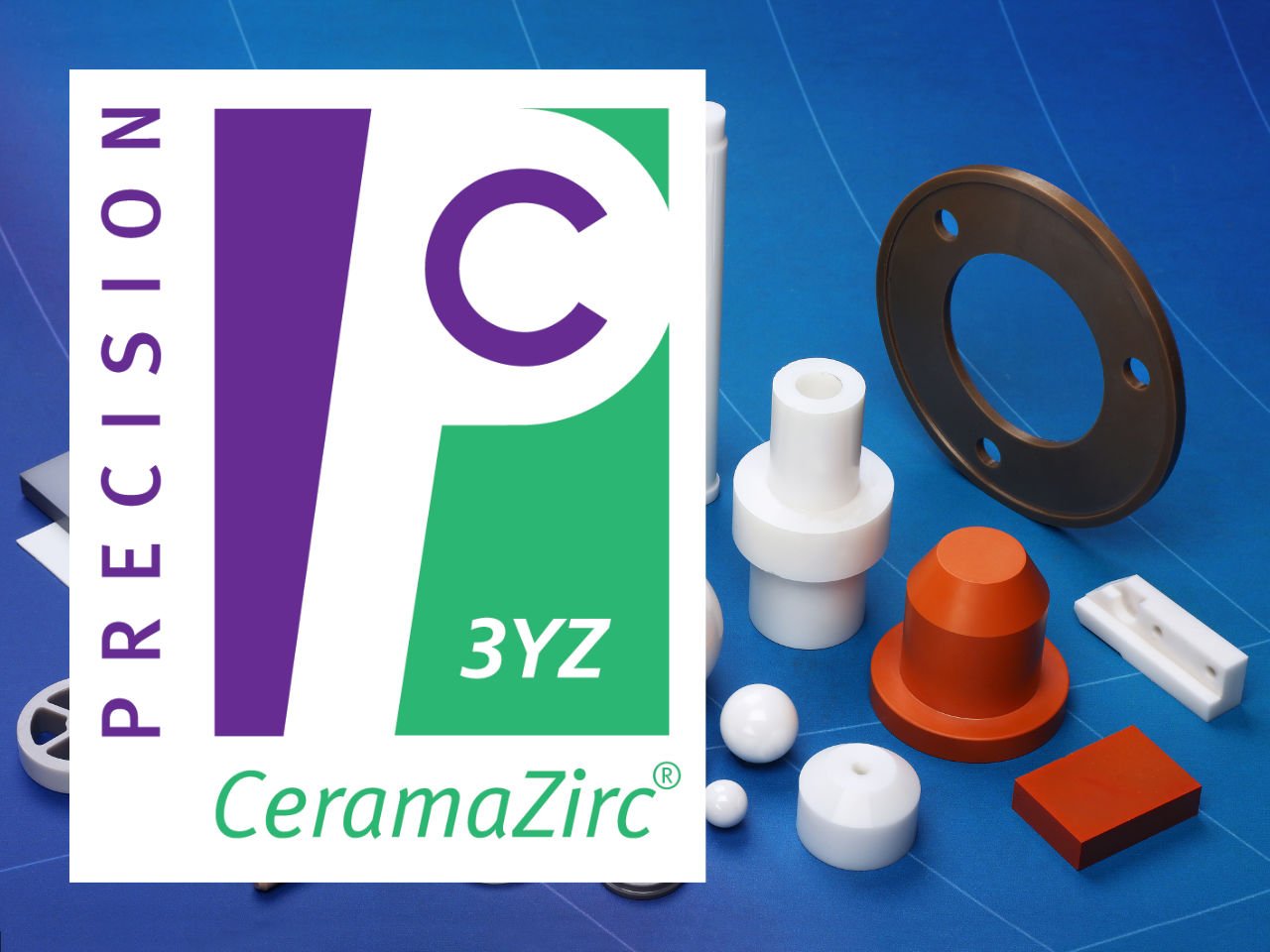
Zirconia (ZrO2) - CeramaZirc™ 3YZ
- Flexural Strength: 1200 MPa
- Key Features: High-purity zirconia with enhanced strength and longevity.
- Best For: Precision-engineered components requiring exceptional durability.
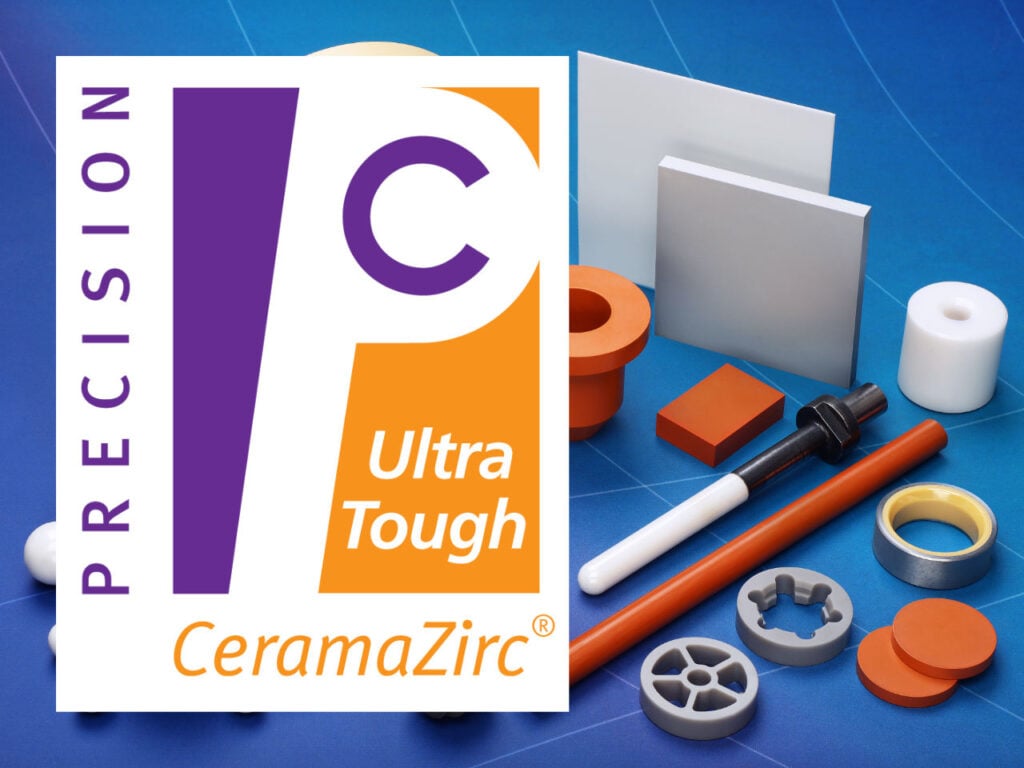
Zirconia (ZrO2) - CeramaZirc™ Ultra Tough
- Flexural Strength: 1000 MPa
- Key Features: Advanced ceramic composite, reinforced with alumina platelets for enhanced toughness.
- Best For: Applications needing superior fracture toughness and resilience.

Silicon Nitride (Si3N4) – CeramaSil-N™ PCSN2000
- Flexural Strength: 970 MPa
- Key Features: Versatile mechanical, thermal, and electrical properties.
- Best For: High-temperature and high-load applications.

Zirconia-Alumina (ZTA) – CeramAlloy™ Ultra Hard
- Flexural Strength: 850 MPa
- Key Features: Combination of high hardness, strength, wear, and corrosion resistance.
- Best For: Industrial applications where toughness and durability are crucial.
How is Flexural Strength Measured?
Flexural strength is usually measured using a method called ‘Modulus of Rupture’ with three or four point bending test methods available. For flexural strength testing of ceramics, the primary standards are ASTM C1161 (ambient temperature) and ASTM C1211 (elevated temperature), with ISO 14704 and ISO 23242 also relevant for specific applications.
Tensile strength will be lower typically around 50-70% of the bending strength. For determining the tensile strength of ceramics, key standards include ASTM C1273 for monolithic advanced ceramics at ambient temperatures, ASTM C1359 for advanced ceramics at elevated temperatures.
Why Choose Advanced Ceramics for High-Flexural Strength Applications?
- Exceptional Durability: Withstand extreme mechanical stress without deformation.
- High Wear & Corrosion Resistance: Ideal for harsh environments and long-term performance.
- Fracture Toughness: Ceramics like Zirconia and Silicon Nitride provide superior toughness compared to conventional materials.
- Electrical and Temperature Resistance: Ceramics can offer electrical insulation and mechanical strength at high temperatures, unlike metals, glasses or polymers.
Get Expert Advice on Choosing the Right Ceramic Material
Choosing the right ceramic material for high-flexural strength applications ensures long-term reliability and optimal performance. Whether you need Zirconia, Silicon Nitride, or Alumina-based ceramics, our materials offer industry-leading strength and durability.
Looking for the best ceramic material for your application? Contact our team for expert recommendations tailored to your needs.
Flexural Strength Material Comparison
Frequently Asked Questions
-
What factors affect flexural strength in ceramics?
Factors include composition, grain size, processing method, defect distribution, surface finish, component size and shape, and sintering conditions.
-
How does zirconia compare to alumina in flexural strength?
Zirconia typically offers higher flexural strength than alumina due to its smaller grain size and superior fracture toughness. Hence zirconia earned the nickname ‘Ceramic Steel’. In addition, it has 50% lower Young’s Modulus (stiffness), resulting in four times the deflection before failure.
-
Is flexural strength the same as tensile strength?
No. Flexural strength measures resistance to bending, while tensile strength measures resistance to pulling forces. Tensile strength is around 50-70% of flexural strength as a rough guide.
-
Can ceramics be engineered to improve flexural strength?
Yes, through techniques like nano-grain refinement, composite reinforcement, and HIPPING (Hot Isostatic Pressing).
Related Properties
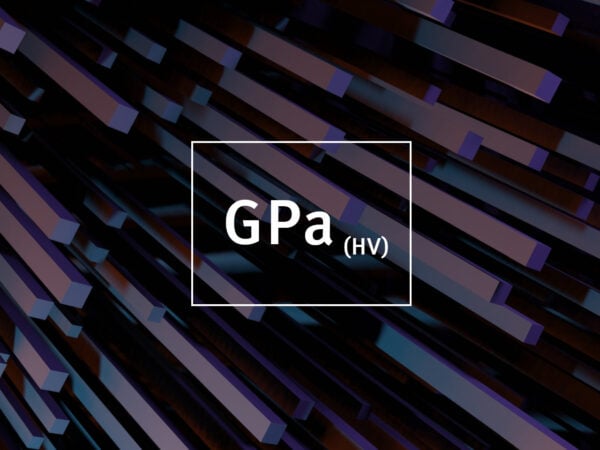
Hardness
One of the most valuable characteristics of advanced ceramics in high-performance applications is their extreme hardness. Hard ceramic materials are used for a wide range of applications in diverse fields and applications such as cutting tools for milling and grinding.

Compressive Strength
Compressive strength is the capacity of a material to withstand loads tending to reduce size. Explained differently, compressive strength resists compression (being pushed together), whereas tensile strength resists tension (being pulled apart).

Fracture Toughness
The ability to resist fracture is a mechanical property of materials known as fracture toughness. For advanced ceramics it uses a critical stress intensity factor known as KIC where the fracture normally occurs at the crack terminations.