Silicon Nitride (Si3N4) – CeramaSil-N™
Material Advantages
- High strength over a large temperature range
- High fracture toughness
- Good flexural strength
- Mechanical fatigue and creep resistant
- Lightweight – Low density
- High hardness and wear resistance, both impingement and frictional modes
- Superior thermal shock resistance
- Low thermal expansion
- Electrical insulator
- Good oxidation resistance
- Good chemical corrosion resistance
- Wear-resistant
- High stiffness
Applications
- Rotating ball bearings and rollers bearings
- Cutting tools
- Engine components: valves, rocker arm pads, seal faces
- Induction heating coil supports
- Turbine blades, vanes, buckets
- Welding and brazing jigs
- Heating element components
- Crucibles
- Metal tube forming rolls and dies
- TIG / Plasma welding nozzles
- Weld positioners
- Precision shafts and axles in high-wear environments
- Thermocouple sheaths and tubes
- Semiconductor process equipment
Material Grades
There are several different methods used to produce Silicon Nitride. Each method produces materials with slightly differing properties.
PCSN1000 – Gas Over-Pressure Sintered
This is the most popular method for producing high-strength and complex geometry silicon nitride components. This method uses a silicon nitride powder that has been mixed with sintering aids to promote liquid phase sintering (typically yttria, magnesium oxide, and/or alumina) as well as binders to improve the mechanical strength of the green ceramic body. The powder is pressed into the desired form and green-machining can take place. The parts are then placed into a furnace that has a pressurized nitrogen atmosphere to aid with densification and prevent the evaporation/decomposition of the silicon, nitrogen, and additives.
Precision Ceramics stocks a range of standard silicon nitride ceramic rods, which are all precision turned to an excellent surface finish. These rods can be used as bearings, pistons, engine components, or in a variety of other assemblies. In addition, Precision Ceramics offers full machining/grinding services for custom silicon nitride component manufacturing.
Applications
- Aerospace applications
- Bearing applications
- Engine wear parts
- Foundry applications
- Mechanical engineering
- Medical components
PCSN2000 – Hot Pressed
HPSN is produced by uniaxially pressing silicon nitride powder with sintering additives while applying heat at the same time. This process requires a special type of press and die. It produces a silicon nitride with excellent mechanical properties. However, only simple shapes can be produced. Because it is impossible to green-machine a component that is hot-pressed, diamond grinding is the only way to create complex geometries. Because of the high costs and difficulties associated with diamond grinding and hot-pressing, its use is typically limited to the production of simple components in small quantities.
Applications
- Aerospace applications
- Chemical plant engineering and construction
- Engine wear parts
- Foundry applications
- Mechanical engineering
- Medical components
PCSN3000 – Hot Isostatic Pressed
This method consolidates the silicon nitride powder by using high pressures and high temperatures. A silicon nitride body with closed porosity is isostatically pressed (uniform pressure on all sides) via an inert gas at up to 2000 bar while the chamber is simultaneously heated. This process effectively squeezes any pores/defects from the material while it is sintering and brings the density closer to theoretical. HIPing improves the mechanical properties and reliability, however, it is an expensive process that is typically only used in very select circumstances.
Applications
- Aerospace applications
- Bearing applications
- Chemical plant engineering and construction
- Engine wear parts
- Foundry applications
- Mechanical engineering
- Medical components
PCSN4000 – Extruded Gas Over-Pressure Sintered
This method uses a silicon nitride powder that has been mixed with sintering aids to promote liquid phase sintering (typically yttria, magnesium oxide, and/or alumina) as well as binders to improve the mechanical strength of the green ceramic body.
Precision Ceramics stocks a range of standard silicon nitride ceramic rods, which are all precision ground to an excellent surface finish. These rods can be used as bearings, pistons, engine components, or in a variety of other assemblies. In addition, Precision Ceramics offers full machining/grinding services for custom silicon nitride component manufacturing.
Applications
- Aerospace applications
- Bearing applications
- Chemical plant engineering and construction
- Engine wear parts
- Foundry applications
- Mechanical engineering
- Medical components
Material Properties
Mechanical Properties
Property | Unit | PCSN1000 | PCSN2000 | PCSN3000 | PCSN4000 |
---|---|---|---|---|---|
Density | g/cm3 | 3.18-3.40 | 3.18-3.40 | 3.18-3.26 | 3.23 |
Compressive Strength | MPa | 3000 | 3000 | 3000 | 3000 |
Flexural Strength @ 25°C | MPa | 730 | 970 | 760-830 | 850 |
Weibull-Modulus m | – | 18 | 20 | 12 | 18 |
Fracture Toughness KIc | MPa m1/2 | 7 | 6.2 | 6.2-6.5 | 8.5 |
Young‘s Modulus | GPa | 300 | 300 | 300-310 | 320 |
Poisson’s Ratio | – | 0.26 | 0.26 | 0.26 | 0.28 |
Hardness | GPa | 15 | 15 | 15.3-15.6 | 16 |
Thermal Properties
Property | Unit | PCSN1000 | PCSN2000 | PCSN3000 | PCSN4000 |
---|---|---|---|---|---|
Thermal Conductivity @ 20°C | W/mK | 25 | 24 | 25 | 28 |
Thermal Shock Parameter R1 | K | 558 | 748 | 590-620 | 700 |
Thermal Shock Parameter R2 | W/m | 14 | 18 | 15 | 19 |
CTE1 25°C ➞ 250°C | 10-6/K | 1.9 | 1.9 | 1.9 | 1.9 |
CTE1 25°C ➞ 1000°C | 10-6/K | 3.2 | 3.2 | 3.2 | 3.2 |
Maximum Temperature (Inert) 2 | °C | 1400 | 1400 | 1400 | 1400 |
Maximum Temperature (Oxidizing) 2 | °C | 1200 | 1200 | 1200 | 1200 |
1 Coefficient of Thermal Expansion (CTE) describes how the size of an object changes with a change in temperature.
2 No load.
Electrical Properties
Property | Unit | PCSN1000 | PCSN2000 | PCSN3000 | PCSN4000 |
---|---|---|---|---|---|
Volume Resistivity @ 25°C | ohm-cm | 1014 | 1014 | 1014 | 1012 |
Dielectric Strength DC @ 25°C | kV/mm | 19 | 19 | 19 | 19 |
Dielectric Constant | 1 MHz | 8 | 8 | 8 | 7 |
Disclaimer: The values presented are mean and typical of those resulted from test samples. They are provided as an indication only to serve as guidance in the design of ceramic components and are not guaranteed in any way. The actual values can vary according to the shape and size of the envisioned component.
Datasheets
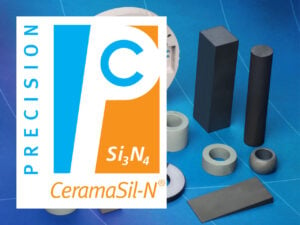
Silicon Nitride
CeramaSil-N
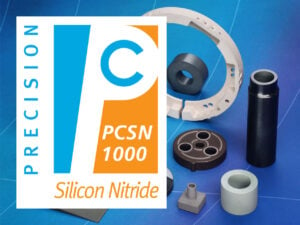
Silicon Nitride
PCSN1000
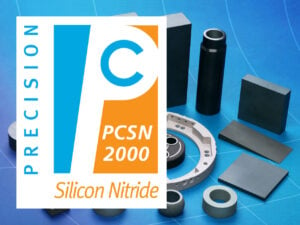
Silicon Nitride
PCSN2000

Silicon Nitride
PCSN3000

Silicon Nitride
PCSN4000
Silicon Nitride Machining
Silicon Nitride can be machined in green, biscuit, or fully dense states. It can be machined relatively easily into complex geometries while in the green or biscuit form. However, the sintering process that is required to fully densify the material causes the silicon nitride body to shrink approximately 20%. This shrinkage means that it is impossible to hold very tight tolerances when machining silicon nitride pre-sintering. In order to achieve very tight tolerances, fully sintered material must be machined/ground with diamond tools. This processes uses a very precise diamond coated tool/wheel to abrade away the material until the desired form is created. This can be a time-consuming and costly process due to the inherent toughness and hardness of the material.
Frequently Asked Questions
-
What is Silicon Nitride used for?
- Rotating ball bearings and rollers bearings
- Cutting tools
- Engine components: valves, rocker arm pads, and seal faces
- Induction heating coil supports
- Turbine blades, vanes, and buckets
- Welding and brazing jigs
- Heating Element components
- Crucibles
- Metal tube forming rolls and dies
- TIG / Plasma welding nozzles
- Weld positioners
- Precision shafts and axles in high-wear environments
- Thermocouple sheaths and tubes
- Semiconductor Process Equipment
-
What are the advantages of Silicon Nitride?
Compared with other technical ceramics, the low thermal expansion coefficient of Silicon Nitride provides good thermal shock resistance. It is extremely hard, fracture-tough, surpasses the high temperature capabilities of most metals, and also has a superior oxidation resistance. As a consequence, silicon nitride can withstand the toughest conditions in the most demanding high-temperature and high-load applications.
Even NASA scientists recognized its unique properties when silicon nitride bearings were used in the main engines of the Space Shuttle. It was identified as one of the few monolithic ceramic materials capable of surviving the severe thermal shock and thermal gradients generated in hydrogen / oxygen rocket engines and proved completely reliable throughout the entire Space Shuttle program.
-
What is the formula for Silicon Nitride?
The formula for silicon nitride is Si3N4.