Macor ® – Machinable Glass Ceramic
Advantages
- Can be machined with normal metalworking tools
- Strong and rigid; unlike high temperature plastics, Macor will not creep or deform
- Low thermal conductivity; useful high temperature insulator
- Electric insulator, especially at high temperatures
- Excellent with high voltages and a broad spectrum of frequencies
- Does not require firing after machining
- Continuous use temperature of 800°C; Peak temperature of 1000°C
- Zero porosity
- Won’t outgas in vacuum environment
- Very tight machining tolerances of up to 0.0005in (0.013mm)
- Excellent dimensional stability in a variety of environments (heat, radiation, etc.)
- Radiation resistant
- Coefficient of thermal expansion readily matches most metals and sealing glasses
Applications
- Precision coil formers (high precision and dimensionally stable)
- High voltage insulators (smooth surface finish and unaffected by arcing)
- Spacers, cavities and reflectors in laser assemblies (precision finish and heat resistant)
- Thermal breaks in high temperature processing equipment
- Coil supports and vacuum feed-throughs (vacuum stable and hermetically sealable)
- Retaining rings on hinges, windows and doors of NASA’s Space Shuttle
- Supports and components in several satellite borne systems (thermally and electronically insulating)
- Fixtures and reference blocks in power generation units (dimensionally unaffected by irradiation)
Macor Material Properties
Mechanical Properties
Macor machinable glass ceramic is strong and rigid. It has zero porosity and can be polished to a smoothness of 0.5µin.
Property | Units | Macor |
---|---|---|
Density | g/cm3 | 2.52 |
Young’s Modulus | GPa | 66.9 |
Poisson’s Ratio | – | 0.29 |
Compressive Strength | MPa | 345 |
Flexural Strength @ 25°C | MPa | 94 |
Fracture Toughness KIc | MPa m1/2 | 1.53 |
Shear Modulus | GPa | 25.5 |
Hardness | GPa | 2.3 |
Thermal Properties
Macor will not creep or deform like high temperature plastics. It has low thermal conductivity, which makes it useful as a high temperature insulator. Macor has excellent dimensional stability in a variety of environments (heat, radiation, etc.). It’s coefficient of thermal expansion readily matches most metals and sealing glasses.
Property | Units | Macor |
---|---|---|
Maximum Temperature (Oxidizing) | °C | 800 |
Maximum Temperature (Inert) | °C | 1000 |
Thermal Conductivity @ 25°C | W/mK | 1.46 |
Specific Heat | kJ/kg°C | 0.79 |
CTE1 25°C ➞ -100°C | 10-6/K | 8.1 |
CTE1 25°C ➞ 300°C | 10-6/K | 9 |
CTE1 25°C ➞ 600°C | 10-6/K | 11.2 |
CTE1 25°C ➞ 800°C | 10-6/K | 12.3 |
1 Coefficient of Thermal Expansion (CTE) describes how the size of an object changes with a change in temperature.
Electrical Properties
Macor machinable glass ceramic is a good electric insulator, especially at high temperatures. It works excellent with high voltages and a broad spectrum of frequencies. It is also radiation resistant.
Property | Units | Macor |
---|---|---|
Resistivity @ 25°C | ohm-cm | 1014 |
Dielectric Constant @ 1KHz | – | 6.01 |
Dielectric Constant @ 8.5 GHz | – | 5.64 |
Loss Tangent | 1 kHz | 0.0040 |
Loss Tangent | 8.5 GHz | 0.0025 |
Dielectric Strength (AC) avg. 25°C, 12 mm thickness | kV/mm | 9.4 |
Dielectric Strength (DC) avg. 25°C, 12 mm thickness | kV/mm | 62.4 |
Volume Resistivity @25°C | ohm-cm | >1017 |
Disclaimer: The values presented are mean and typical of those resulted from test samples. They are provided as an indication only to serve as guidance in the design of ceramic components and are not guaranteed in any way. The actual values can vary according to the shape and size of the envisioned component.
Datasheet
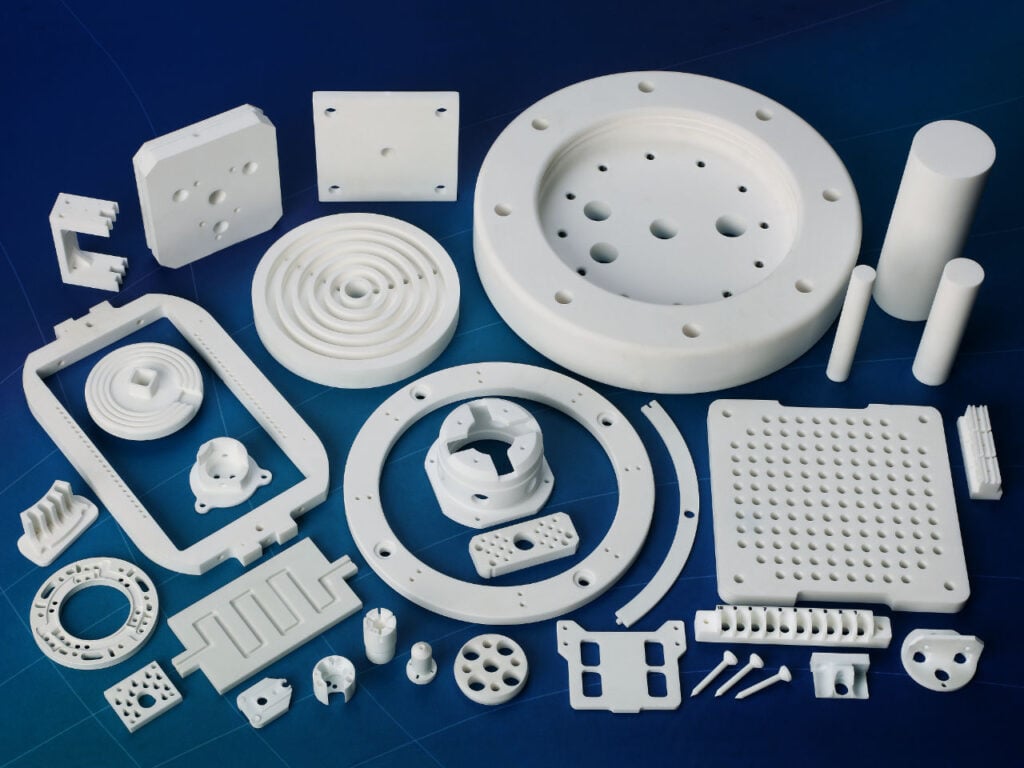
Macor
Machinable Glass Ceramic
Macor Machining
Macor is one of the few ceramics that can be machined using regular metal working tools. While there is a learning curve to machining Macor, it is certainly achievable for someone with the correct skills and patience. The machining characteristics of Macor are very different from metals and plastics so we recommend you take some time to practice drilling, turning, and milling the Macor before you try to make your own component to understand how it behaves. Unlike plastics and metals, ceramics never plastically deform; this means that when machining Macor you must be very conscious of chipping.
Precision Ceramics is your Macor machinable glass ceramic specialist for your technical ceramic prototyping & manufacturing needs. We are always happy to use our many years of advanced ceramics experience to provide advice on materials, design, and application. If you would like to buy Macor plates, rods, bars, tubes, or custom machined components please contact us and one of our experts will be happy to assist you.
Macor Manufacturing Process
This latest promotional video from Corning shows the complex manufacturing process for Macor through to final applications.
Frequently Asked Questions
-
What's the difference between Macor and Shapal?
Shapal Hi M Soft and Macor glass ceramic are often compared because they both are machinable ceramics, however, both of these materials have significantly different mechanical and thermal properties. The following are som factors to consider when choosing between Macor and Shapal.
Thermal Conductivity
Shapal Hi M is a thermal conductor at 90 W/(m K), Macor is a thermal insulator with a thermal conductivity of 1.46 W/(m K)
Thermal Cycle
Shapal is not prone to suffering from thermal shock failures while Macor is vulnerable to thermal shock – if the parts have rapid heat up and cool down cycles then Shapal is a better option.
Maximum Temperature
Shapal has a much higher maximum use temperature of 1900C (in an inert atmosphere) and 1000C (in air).
Strength
Shapal offers better bending strength (300 vs 94 MPa) as well as better compressive strength ( 1200 vs 345 MPa) when compared with Macor.
Cost
Macor is a cheaper material that Shapal Hi M Soft, if it can be used instead of Shapal the user will typically see significant cost reductions.
-
What's the difference between Macor and Alumina?
Alumina is a very commonly used technical ceramic due to its versatile properties, however, because it is such a hard material extensive diamond grinding is often required making it costly to produce in small quantities. Macor Machinable Glass Ceramic is often a viable alternative that can allows for significantly reduced production costs. The following are some factors to consider when choosing between Macor and Alumina.
Thermal Cycle
Macor is vulnerable to thermal shock – if you have rapid heat up and cool down cycles Macor may not be appropriate. Shapal may be a viable alternative.
Maximum Temperature
Macor has a maximum use temperature of 1000C (unstressed) and 800C (stressed); Alumina does offer higher temperature capabilities.
Wear Resistance
The same feature that makes Macor machinable means that it has relatively poor wear resistance when compared with Alumina.
Cost
For smaller quantities Macor often offers significant price reductions than Alumina components.
-
What is Macor made of?
Macor is a composite material made of fluorophlogopite (a type of Mica) in a borosilicate glass matrix (such as used in test tubes and Pyrex®) in a ratio of 45/55 respectively. The randomized microcrystalline structure allows tools to excavate micron-sized portions without cracking and fracture, leading to very exacting tolerances. Macor is composed of:
- 46% silica (SiO2)
- 17% magnesium oxide (MgO)
- 16% aluminium oxide (Al2O3)
- 10% potassium (K2O)
- 7% boron (B2O3)
- 4% fluorine (F)
-
What factors should I consider when using Macor?
Macor is vulnerable to halogen acids such as HCl (hydrochloric acid), although not a flash failure or sudden deterioration. Tests show a 2.52 gram sample (1cc) of Macor exposed to Hydrochloric Acid at a pH of 0.1 experienced a 100 mg loss, or 3.96% over 24 hours. Exposed to Sodium Hydroxide at a pH of 13.2 it experienced a loss of 0.396% in six hours. It is stable to 1000°C in air, and to 600°C in vacuum. Beyond 600°C (in vacuum) fluorine evolution will occur manifesting as boron trifluoride or hydrofluoric acid.
The most commonly available size of Macor is 12.5″ x 12.5″ x 2.125″ (317 x 317 x 54mm).
-
Can Macor be joined?
Macor can be connected and joined with a variety of methods. If it is metalized (metal inks or sputtering) it can be soldered, or brazed to other pieces, or bound to metal pieces such as titanium in the image to the right. Epoxy provides a strong joint and sealing glass provides a hermetic seal. Macor can even be lapped and bound with a convention mechanical connection. With its remarkably tight machining tolerances of up to 0.0005in (0.013mm), joining is a simple and straightforward task. It’s coefficient of thermal expansion readily matches most metals and sealing glasses. With appropriate polishing it can have a surface finish of less than 20 μinches, or 0.5 μmeters.
-
Is Macor good for prototyping?
Macor machinable glass ceramic is an incredibly versatile material that can quickly be made into very complex geometries. Because of it’s excellent machinability, Macor allows for rapid ceramic prototyping with many different iterations able to me made in a short period of time.
-
What is Macor Machinable Glass Ceramic used for?
Macor machinable glass ceramic was originally designed for NASA’s space shuttle to prevent thermal transfer from the exterior to the inside of the vehicle. It was used in the window frames of the space shuttle because of its electrical and heat insulating qualities; because of its radiation resistance and non-porosity (it has a porosity of zero); and because it emits no vapors (toxic or otherwise) of any kind, especially at the lower pressures that were found in spacecraft. Macor is an excellent material for high vacuum applications, such as electron microscopy, because when properly baked out, it cannot outgas at any achievable vacuum level.
Electronics / Semiconductors
- Precision coil formers (high precision and dimensionally stable)
- High voltage insulators (smooth surface finish and unaffected by arcing)
Laser Applications
- Spacers, cavities and reflectors in laser assemblies (precision finish and heat resistant)
High Vacuum Applications
- Thermal breaks in high temperature processing equipment.
- Coil supports and vacuum feed-throughs (vacuum stable and hermetically sealable)
Aerospace / Space Industry
- Retaining rings on hinges, windows and doors of NASA’s Space Shuttle
- Supports and components in several satellite borne systems (thermally and electronically insulating)
Nuclear Industry
- Fixtures and reference blocks in power generation units (dimensionally unaffected by irradiation)
-
What is the maximum size of Macor I can purchase?
300mm x300mm x 55mm is the maximum size and we can supply any smaller size or shape on request. We also carry many standard sizes of Macor bar, rod and sheet in stock for quick delivery. We are happy to discuss supplying fully machined components produced in our in-house facility. A thickness of 60mm may be possible in some applications.
-
What is the maximum working temperature of Macor?
Macor begins to soften at 1,000°C so for continuous use we would recommend a maximum working temperature of 850’C. We have other ceramics that can be used under load at over 2,000°C.