What design and material considerations are there from an application and advanced ceramics manufacturing perspective?
Whether you’re manufacturing advanced ceramics, or any other material, defining what you need for the application is the crucial first step. You are likely to need to consider several key properties for your application.
These key properties dictate not only the general materials composition but also the specific grade of the material chosen. We will also need to consider the manufacturing route for that design – and how you manufacture advanced ceramics depends on the shape, quantity required and final application factors.
This can be a bit of a puzzle and it’s often best to consult experts to get early advice. It is common to have a non-disclosure agreement signed at this stage to allow details to be shared from both sides.
So, what should you consider? Well, start with the primary properties – whether it’s electrical, thermal, mechanical, optical, or something else entirely. Then think about the secondary requirements. You may be focused on electrical performance, but do your ceramics also need to withstand mechanical stresses? And don’t forget the tertiary properties, like handling high temperatures or particular atmospheres.
And here’s a list of other things to ponder: production volume, joining requirements, expansion coefficients (low or high), material cost, shaping options, tolerances and more. It’s like a checklist for creating the perfect design. So remember, when it comes to ceramics, it’s all about getting the right fit for your needs.
A rule of thumb is that, typically, ceramic components need to satisfy at least 3 difficult application requirements, to justify the ceramic material selection over polymers or metals.
How are sintered ceramics shaped and what tolerances are possible?
When it comes to advanced ceramics manufacturing there are many methods available and finding the best value process depends on the shape, performance and tolerances. Here are some of the classic approaches.
Die Pressing
This is the budget-friendly option and is fast and efficient. Often considered industry’s favourite route, it works best with simple shapes and when the height to diameter ratio isn’t too large. Think small components such as ceramic sealing discs, ceramic magnets and tiles.
Isostatic Pressing
Not as speedy as die pressing, but it’s great for larger parts and complex shapes; a classic example is the spark plug. There are different types of isostatic pressing, each with its pros and cons, like dry and wet bag, cold and hot isostatic pressing. Perfect for small quantities and for volume production.
Injection Moulding
Borrowed from the plastics world, this one’s for complex shapes in high volume quantities. Tooling costs are much more appreciable, so it’s not ideal for small batches. The production speed is high, but burning out all the polymer binder can really slow things down and make dimensional control trickier – say +/- 5%.
Extrusion
This is the go-to method for tubes and rods, and tooling costs are manageable. You can even find standard stock over a range of sizes available in materials like 99.7% alumina.
Slip Casting
Tape Casting
This one’s perfect for flat ceramic sheets, especially for substrates for electronics. You can often find a variety of thicknesses in stock, especially in alumina and aluminium nitride.
Turning that “green body”, an unfired ceramic, into something that is solid and usually, but not always, fully dense, is the final transformation and involves sintering. This is carried out in batch or continuous furnaces in air or in a protective atmosphere for the non-oxide ceramics. There are also new tricks for this, like field-assisted sintering and spark plasma sintering . Sometimes, a little pressure is needed, and that’s when hot pressing or hot isostatic pressing, known as HIPing, steps in. HIPing can be great to reduce defects and increase overall mechanical properties, though at increased cost, and can change the colour of the ceramic.
For the future – we will see additive manufacturing of ceramics. It’s already working well with polymers and metals, and ceramics are next in line. There are plenty of projects in development.
Now, when it comes to tooling, it may be worth investing in the right set of tools for a big project. The supplier usually takes the lead in designing the tooling, owns it and maintains it.
The manufacturing method might switch gears when you go from prototypes to production. And that can affect the final properties and tolerances, so expect some testing along the way.
Tape cast materials offer flexibility. You can shape them after firing with laser cutting or even stamp a shape from them before firing when they are still soft. They can stack up, get pressed and be co-fired together as layers.
Tight tolerances will mean great cost, as you will often need diamond grinding, polishing or lapping processes after firing to achieve tolerances. Some features will be easier to grind, such as outside diameters, others may be difficult or slow.
So, when considering the design and manufacture of ceramics, it is helpful to get advice early, to ensure the right blend of tools and techniques.
Andy Duncan & Precision Ceramics
Andy Duncan, Business Development Director at Precision Ceramics, has spent over 30 years in Engineering Ceramics within Technical Management and Business Development roles. Andy’s ceramics application experience is broad, spanning the design and selection of ceramic materials to metal joining, and piezoceramics. Combined with diverse application and design knowledge in various markets, Andy can help guide you towards the best-suited material for your application.
Precision Ceramics is a leader in supplying customized technical ceramics solutions. We go beyond mere manufacturing – we partner with you at every stage of material selection, product design, and development.
If you have any questions regarding which ceramic material might be best for your application, please don’t hesitate to contact us.
Related Topics

Ceramic Manufacturing Process
In this video blog we unlock the secrets to cost-effective, volume dependant ceramic manufacturing. Learn how quantity, design, and material selection could save you time and money on your next ceramic project!
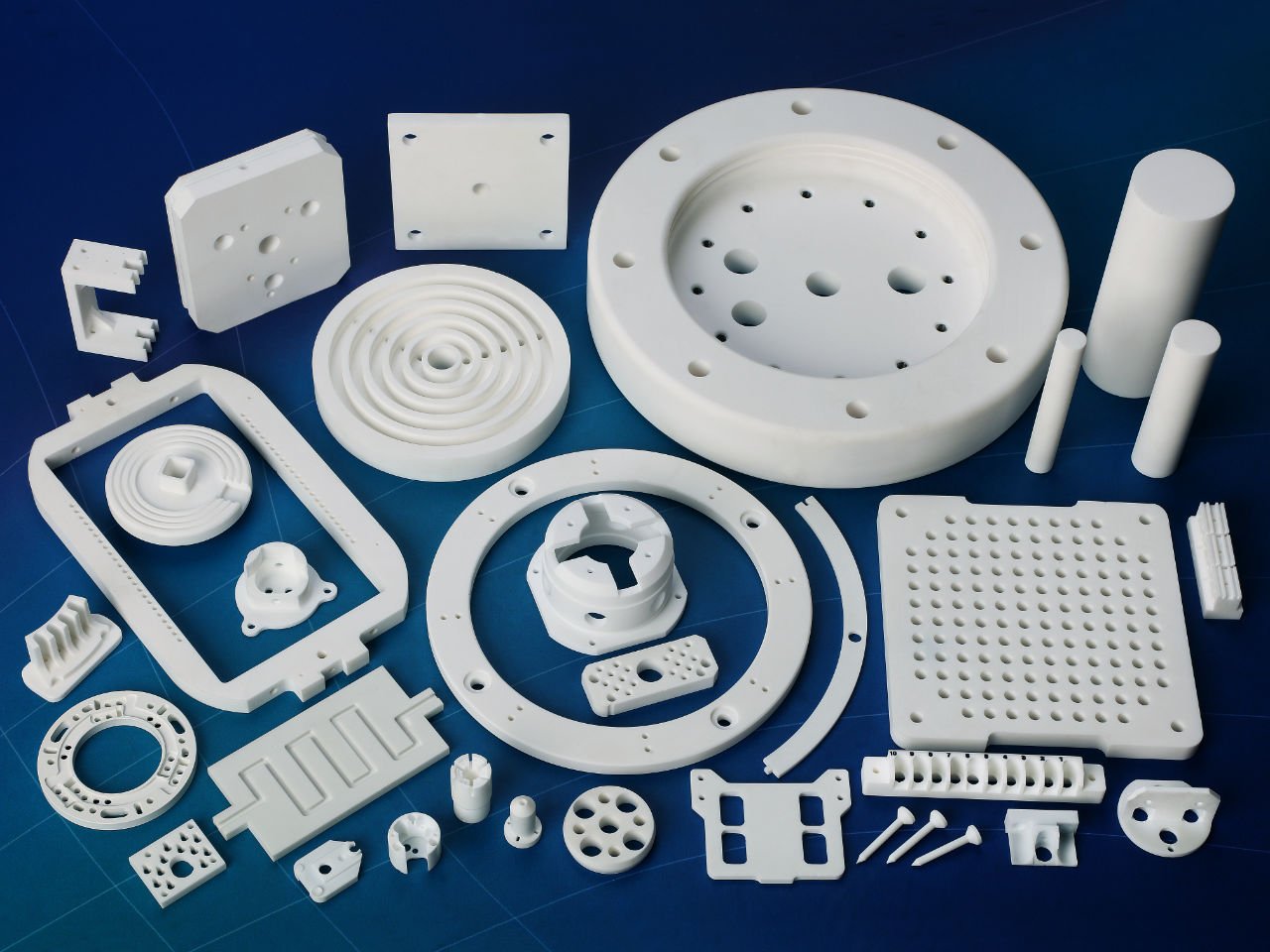
Materials
Precision Ceramics offers a wide range of advanced advanced ceramic materials to ensure that we have the right material for your application.
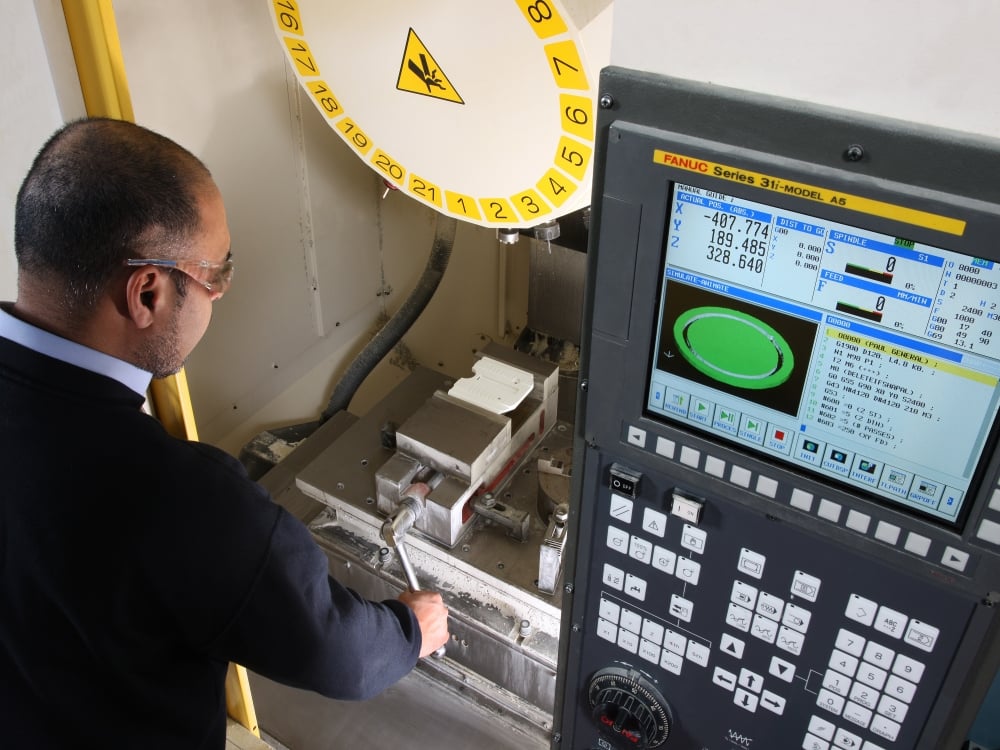
Technical Ceramic Manufacturing
Precision Ceramics is an accomplished authority in custom ceramic component engineering & design support.