How does quantity influence tooling costs and the ceramic manufacturing process?
The tighter your tolerances, the more it will cost. So, it’s a good idea to keep those tolerances in check and not to go overboard. Less is often more in this game.
When converting a plastic or metallic part to a ceramic material, you may require a simplification of the shape and relaxing of tolerances.
Remember, the name of the game is efficiency and cost-effectiveness.
The best ceramic designs are simpler, symmetrical shapes, with relaxed tolerances. A ceramic friendly design will make a huge difference when making ceramics in quantity.
What are machinable ceramics and their pros and cons?
Popular machinable ceramics include Macor, Shapal and Boron Nitride – they’re softer ceramics and you can machine them with carbide tools, and no post-firing is required. This provides a shortcut to making ceramic parts.
These machinable materials are ideal for prototyping and small batches. The properties might even work for your final application. But when you need high quantities, they can get comparatively pricey. So the pricing advantage in low quantities is reversed.
How does the design influence the properties of the ceramic?
Engineering ceramics are stiff and robust, but they’re also sensitive to small defects, such as tiny pores. So, smaller components with polished surfaces tend to be stronger. Watch out for sharp edges and thin sections – they can be a bit fragile and prone to chipping.
Let’s talk design. Good design is not just about the ceramic itself; it’s also how you put the whole thing together. You want to limit any residual stress, whether from manufacturing or in use. Compressive stress is the friendly kind. Tensile and shear stresses need to be kept to a minimum.
If you want even more toughness, you can choose ceramics like Zirconia and Silicon Nitride. They can take on application stresses really well and hence you can find them in blades, welding tools and jigs, just to name a few.
What are the typical lead times involved in the ceramic manufacturing process?
Lead time can range from a quick 1 week to over 20 weeks. That’s a pretty wide spectrum. The longer lead times are partly about the factory’s capacity and about orders stacking up in the queue, and partly about all the different steps needed to make a ceramic component. Sometimes, there can be a dozen or even fourteen steps in the process.

If you need new die press or injection moulding tooling, that’s a whole other story. Just getting those tools ready can take 2 to 3 months before you even start making the parts. So, when you’re in the prototype phase, testing and tweaking, a ceramic project can easily stretch out to 6 to 12 months before you’re receiving production quantities.
So, remember, ceramics aren’t about speed – they’re about precision and patience.
Andy Duncan & Precision Ceramics
Andy Duncan, Business Development Director at Precision Ceramics, has spent over 30 years in Engineering Ceramics within Technical Management and Business Development roles. Andy’s ceramics application experience is broad, spanning the design and selection of ceramic materials to metal joining, and piezoceramics. Combined with diverse application and design knowledge in various markets, Andy can help guide you towards the best-suited material for your application.
Precision Ceramics is a leader in supplying customized technical ceramics solutions. We go beyond mere manufacturing – we partner with you at every stage of material selection, product design, and development.
If you have any questions regarding which ceramic material might be best for your application, please don’t hesitate to contact us.
Related Topics

Advanced Ceramic Manufacturing
In this video blog we delve into the essential design and materials considerations from both application and manufacturing perspectives.
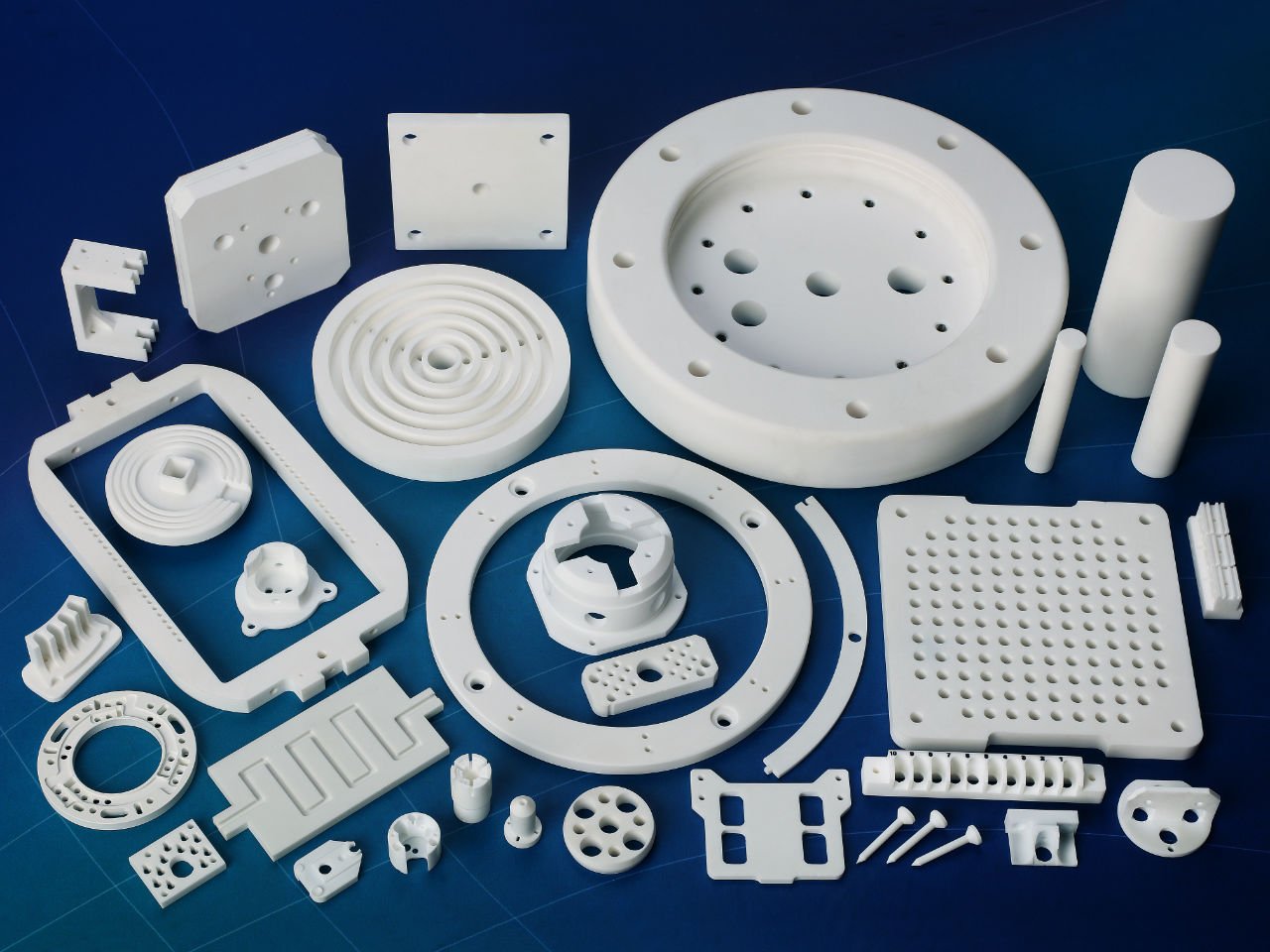
Materials
Precision Ceramics offers a wide range of advanced advanced ceramic materials to ensure that we have the right material for your application.
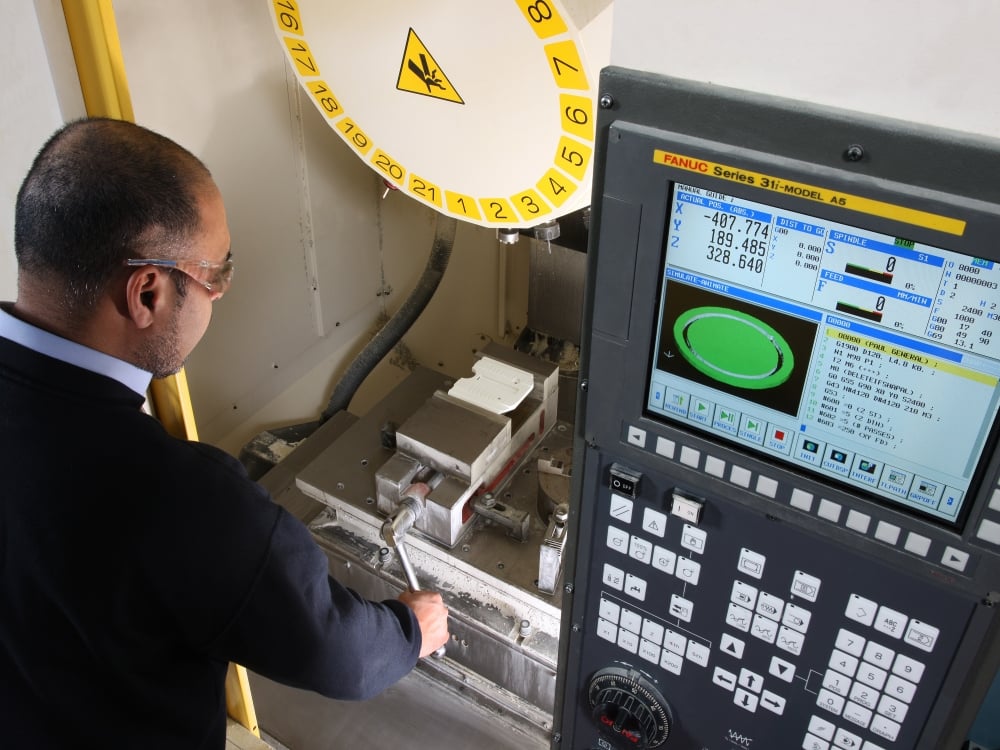
Technical Ceramic Manufacturing
Precision Ceramics is an accomplished authority in custom ceramic component engineering & design support.