How do ceramic materials perform against sliding, abrasive or impact wear?
Ceramics are inherently very wear resistant due to their extreme hardness. These materials have values close to the hardest known material, diamond. They have also the capability to be machined to have extremely smooth surfaces which is very useful for applications such as artificial hip joints or even pseudo surface porosity. This is great for creating lubrication pockets or minimizing surface contact area.
Ceramics also have inherently low friction. Take Silicon Carbide, for instance. It has especially low friction and is very good for sliding wear, such as in mechanical seal faces.
Alumina is one of the great all-around wear resistant ceramics. It’s very versatile, and so is used in a wide range of applications from mixer tap sliding faces and bearing faces to shafts.
It is also a particularly cost-effective ceramic, so presents a good starting point for new designs and won’t break the bank.
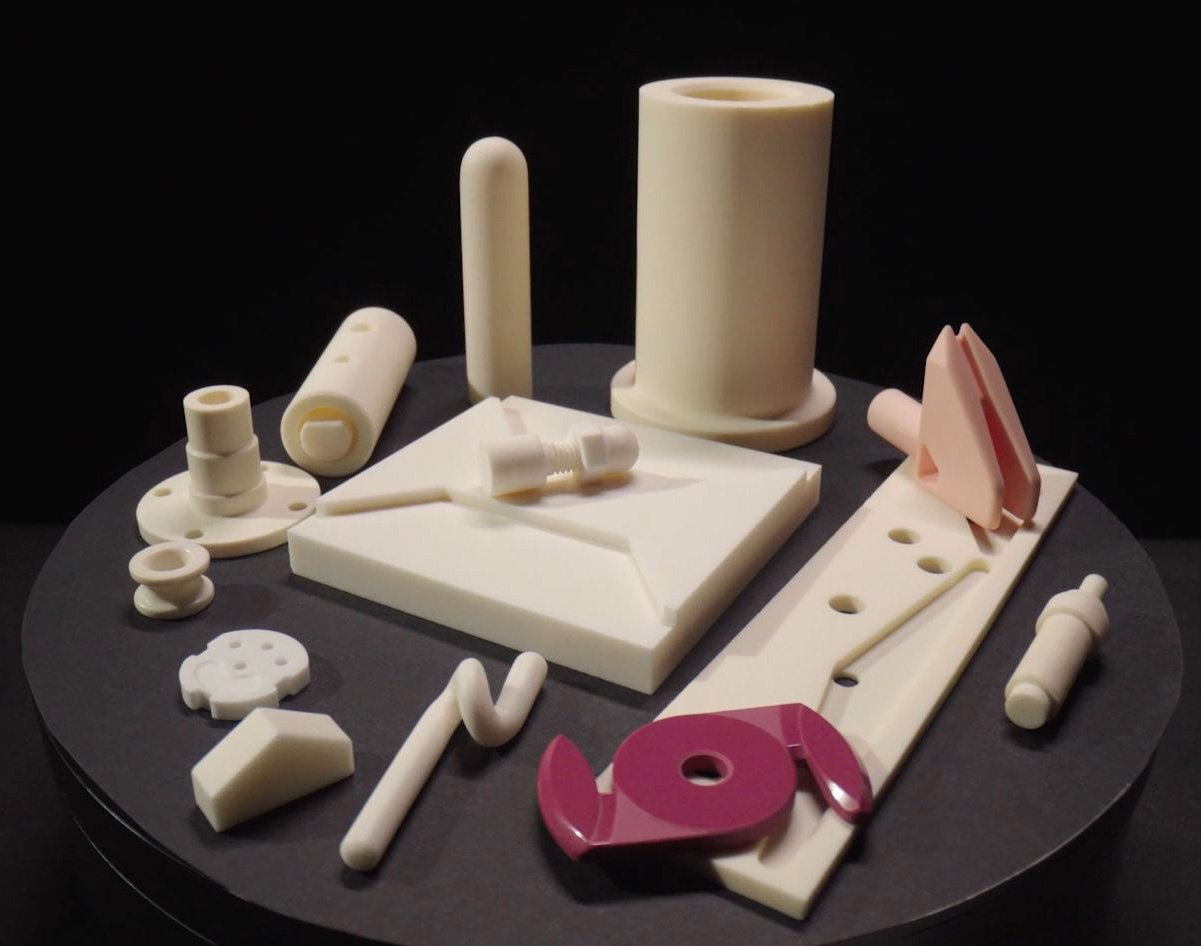
Ceramic or other low friction material coatings may also be very helpful. For example, there are coatings made from diamond like carbon, tungsten disulfide, molybdenum disulfide and the polymer PTFE, better known as Teflon. Coatings need to be chosen that have the right coefficient of thermal expansion for the parent material and good adhesion.
Note, however, that coatings may not work well if the component becomes hot. Some plastics (such as Teflon) only work well for fairly low temperature applications.

Carbon or carbon fiber composites can also be used to run against a ceramic as a sacrificial softer working face or seal.
Do we need different ceramics for different types of wear or specific applications?
Choosing ceramics for wear applications actually means considering a whole range of different factors. It’s not just about wear resistance. There’s a whole checklist of other traits that might be needed.
Take sliding wear, for instance. The material not only needs to be tough and mechanically strong but also needs to survive fatigue, thermal stresses. It might need to be non-magnetic or electrically insulating .
Typical ceramics that are considered are Alumina and Silicon Carbide. While for impact wear the options can include Silicon Nitride and Zirconia.

Ceramics are also kinder against softer seal materials such as carbon and polymers and generally cause less wear than metals. For this reason, ceramics are being increasingly used in human joint replacements, such as hip, knee, and finger joints.

A ceramic may run against another ceramic with little or no lubrication. This is particularly helpful in space applications since lubricants evaporate and hence cannot be used, while metal components can cold weld to themselves.
In general, ceramics usually offer the greatest reliability and durability, combined with low maintenance and low overall life costs for wear applications.


Professor Jon Binner & Precision Ceramics
Professor Jon Binner, esteemed academic at the University of Birmingham renowned for his contributions to the field of ceramics, has joined forces with Precision Ceramics to produce a series of enlightening explainer videos on advanced ceramic materials.
With a wealth of experience demonstrated through numerous peer-reviewed papers, edited books, and patents to his name, Professor Binner brings unparalleled expertise to the collaboration.
His longstanding relationship with Precision Ceramics underscores his commitment to advancing knowledge in the realm of ceramic materials. Thrilled to participate in a project aimed at educating and informing audiences about the intricacies of ceramics, Professor Binner’s involvement promises to offer valuable insights into this vital area of materials science.
Precision Ceramics is a leader in supplying customized technical ceramics solutions. We go beyond mere manufacturing – we partner with you at every stage of material selection, product design, and development.
If you have any questions regarding which ceramic material might be best for your application, please don’t hesitate to contact us.
Related topics:
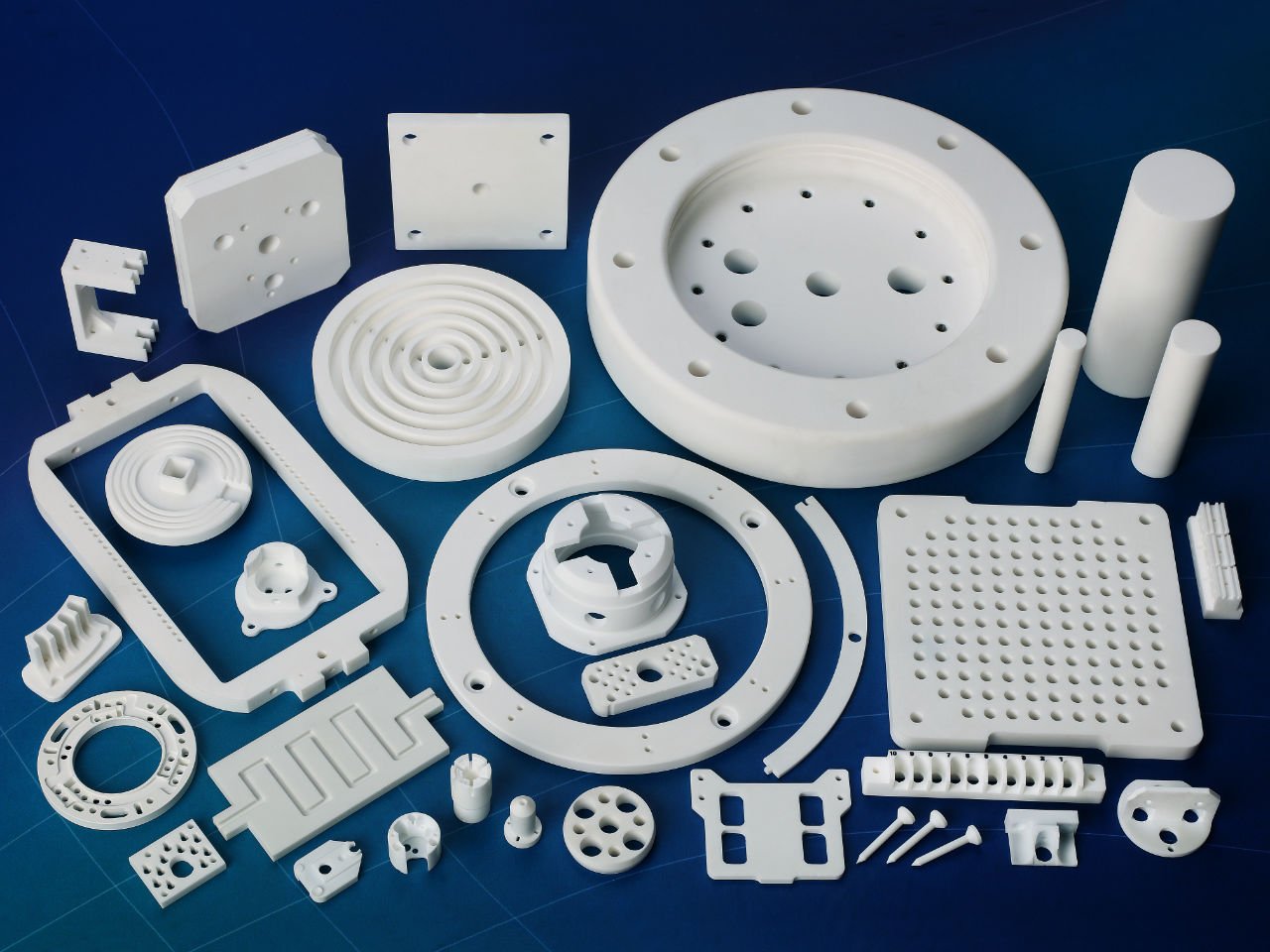
Materials
Precision Ceramics offers a wide range of advanced advanced ceramic materials to ensure that we have the right material for your application.
Ceramic Material Properties
View the mechanical, thermal, and electrical properties to identify which materials best suit your application based on their characteristics.