Ceramic Engineering – As Old As Learning – As Universal As Time …
Ceramic engineering is most commonly attributed to the science and technology of creating objects from inorganic, non-metallic materials. This is done either by the action of heat or at lower temperatures using precipitation reactions from high-purity chemical solutions. The term includes the purification of raw materials, the study and production of the chemical compounds concerned, their formation into components and the study of their structure, composition and properties.
For Precision Ceramics, the term ‘Ceramic Engineering’ takes on a whole new meaning. And whilst the history and science behind the technical ceramics which form the backbone of the company’s business is well recognised, the ‘engineering’ of these materials is much more of a local buzzword for turning them into the widest possible range of technical components for the equally wide field of industries the company serves. Precision Ceramics has a range of advanced ceramic materials catering to these industries.
For aerospace, automotive, defence and dentistry. For domestic households, electronics and opto-electronics. For energy and power generation, foundry and medical applications. And for nuclear power, offshore oil and gas and transportation.
All have two factors in common; the quality and reliability of the technical ceramic products developed for them.
The word ‘ceramic’ is derived from the Greek word κεραμικός (keramikos) meaning pottery. It is related to the older Indo-European language root ‘to burn’ and, as such, ‘ceramic’ may be used as a noun in the singular to refer to a ceramic material or the product of ceramic manufacture.
Not a lot different at Precision Ceramics then – both the name of the company and the name of the company’s principal product.
Early Pioneers

From left to right – Early Ceramic Pioneers: Josiah Wedgwood, Edward Goodrich Acheson and Henri Moissan.
W.H. Nernst developed cubic-stabilized zirconia in the 1920s in Berlin. Amongst other applications, this material is used as an oxygen sensor in exhaust systems.
Ceramic materials may have a crystalline or partly crystalline structure, with long-range order on atomic scale. Glass ceramics may have an amorphous or glassy structure, with limited or short-range atomic order. They are either formed from a molten mass that solidifies on cooling, formed and matured by the action of heat, or chemically synthesized at low temperatures.
As has already been mentioned, the special character of ceramic materials gives rise to many applications as has already been mentioned. As ceramics are heat resistant, they can be used for many tasks that materials like metal and polymers are unsuitable for.
Further Developments
And so the story continues … From the dawn of time in Ancient Greece through the early pioneers of pottery to the highest performance ceramics now available to man, ‘Ceramic Engineering’ continues to shape the world around us in in many aspects of our everyday lives.
Related Topics:
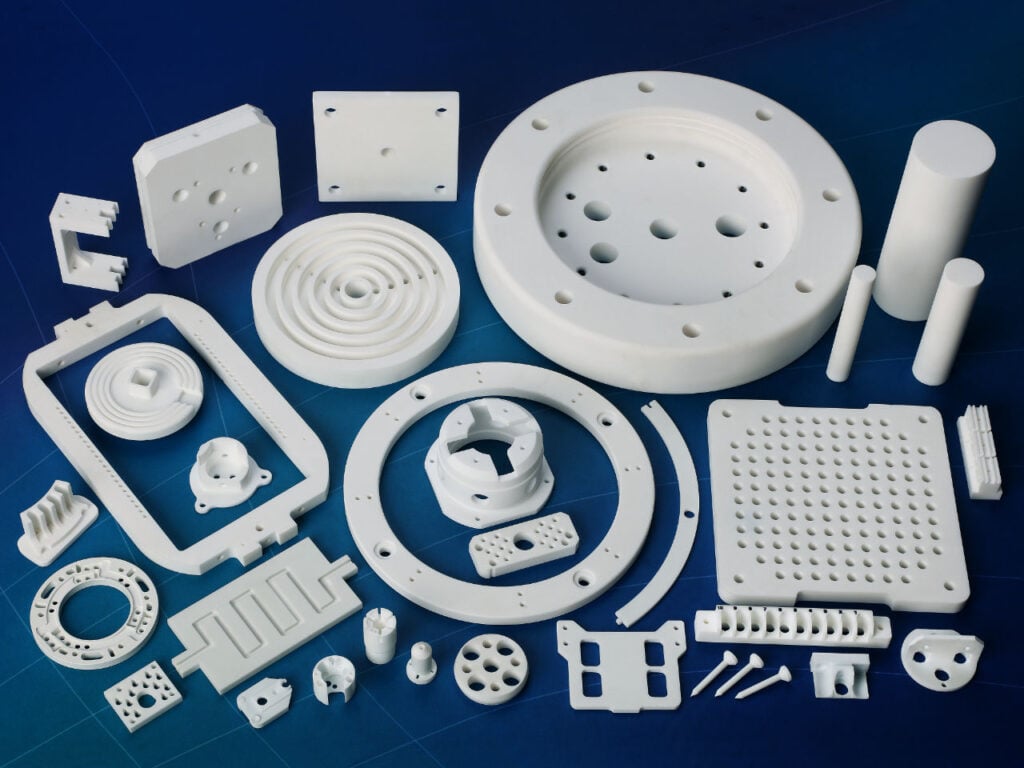
Materials
Precision Ceramics offers a wide range of advanced advanced ceramic materials to ensure that we have the right material for your application.
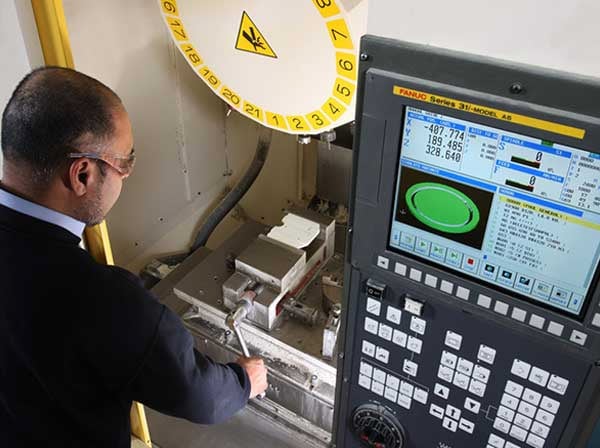
Advanced Ceramic Manufacturing
Precision Ceramics is internationally renowned as as one of the world’s authorities in custom ceramic component engineering & design support.